Why It’s Important to Fail Fast With Product Development
We often think failure is the end point. However, product development failure is actually essential to create better products and stimulate stronger innovation.
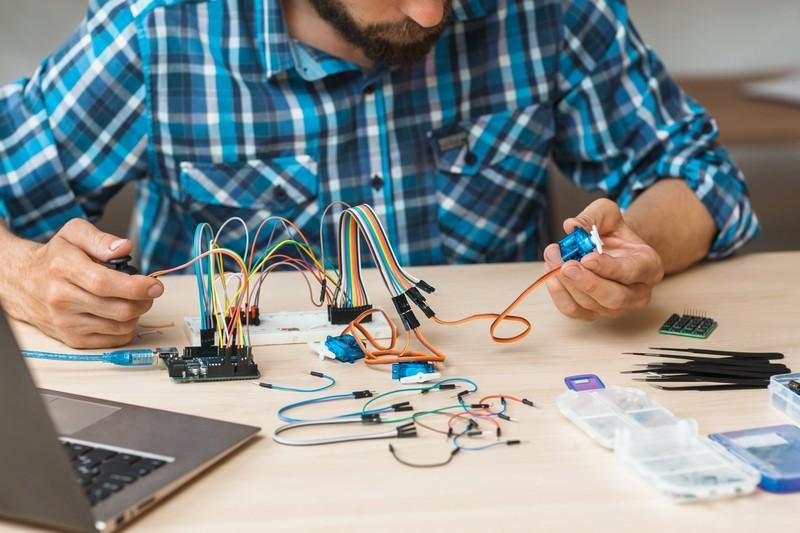
Failing fast means quickly developing a hardware product and testing it rapidly to get answers and feedback regarding its function and results. All bugs and mishaps can then be quickly fixed in the next version of the product.
It does take time and plenty of work to bring a product to the market. Yet, the existence of 3D printers has made rapid hardware development much more common in recent years.
It can take less than a day to build and develop a prototype using a 3D printer.
With this in mind, an engineer can quickly check for any anomalies or problems. By tweaking the design electronically, they can create a better prototype within another couple of days.
Essentially, 3D printers have provided engineers the opportunity to implement a rapid failing fast process in hardware development.
If you purchase your own 3D printer then you can really iterate at super speed. You can literally discover a new problem, design a fix for it, and have a new prototype in your hands to test all in the same day.
Unfortunately, there is no comparable equivalent (yet) to 3D printing for the electronics, so failing fast on the electronics becomes considerably more difficult.
The Challenges of Failing Fast with Electronics
Failing fast and building prototypes for electronics products can be rather challenging. Engineers worldwide have used protoboards for prototyping needs for about the last 50 years.
With perfboards you can solder different parts together to develop your electronics product prototype.
These tools, however, came onto the scene before the invention of surface mount technology and can be rather dated for today’s challenges. Now, the vast majority of designs utilize surface mount technology.
Soldering of Surface-Mount Technology (SMT) components can complicate prototyping and failing fast on the electronics.
The largest challenge when it comes to surface mount components is that prototyping using these components is complex and/or more expensive.
Nonetheless, there are specific approaches you can use to work with surface mount components properly.
Managing Surface Mount Components
If you have a part in your hardware product that comes in a Ball-Grid Array style, you will need specific tools and skills to solder this portion by hand.
When you work with a part like this on surface mount components there are three approaches you can take.
- Purchasing a development board
- Applying solder paste with a stencil and using a temperature-controlled oven
- Outsourcing the soldering process
Outsourcing can be a time-consuming and expensive choice. As such, buying development boards from the component manufacturer may be the better choice in this case.
You can also find low-cost development board options from third-party suppliers.
Hardware and Product Development Cycle
The product development life cycle goes through several different stages. The introductory stage consists of the first time your particular hardware product enters the market for sale.
This is when you begin to promote your brand, identify your customer base, establish your price, and deliver on all intellectual property rights.
The growth stage is when your profit expands, and your brand awareness extends beyond your initial customer base.
The maturity stage is all about stabilization and remaining steady while your sales reach their ultimate peak.
Finally, the decline stage is when you may see a slow decrease in your sales and profits. To prevent this from happening, you should continue to improve the features of the product and reduce the manufacturing and sale prices.
The only way to continuously improve your product is through frequent, easy testing. You can find new product solutions that are more efficient and cheaper to manufacture, but only if you undergo regular product testing.
Design Your Product for Easy Testing
It’s easy to focus on the best features of your electronics and hardware product prototypes, but you’ll need to design it in a way that makes it easy to test out any flaws or problems.
You may have made one prototype that has worked perfectly, but you need to replicate this success.
It’s important to include proper test points on your PCB design for easy testing during development and production.
You will need to make additional prototypes to also test out to ensure the design is reliable and offers consistent performance. If you can achieve the same results as with your original prototype, then your product is one step closer to going on the market.
If you design your prototypes with testability in mind, you should have specific test points on every necessary power and signal portion of the design that you can easily tweak.
Test Early and Test Often
For your manufacturing company to be truly successful, you’ll want to implement an Automatic Optical Inspection step and an Electrical Test step.
In this case, the Automatic Optical Inspection will test your design based on your original outline while the Electrical Test will check any potential errors on your open or short circuits.
As such, your prototype will undergo multiple early tests to check how well it functions. This step is vital to perform before a product reaches the assembly line and hits the market.
With regular and early testing, you can handle any flaws or errors and fix them well ahead of the production deadline.
The Components You Should Test
The main components you will need to test in your hardware prototype are power; microcontrollers or microprocessors; signals and sensors; and user interfaces.
How your prototype is powered is essential, and you’ll need to make sure your design is obtaining the correct voltages when turned on. Troubleshooting voltage problems is critical before you can move on to other parts of the design.
The microcontrollers are the brain of your operation and will need to have the correct code to operate properly. You can use an In-System Programmer (ISP) to program and test this portion of the prototype.
When checking the signals, you’ll need to test the voltage levels and waveforms as well as engage with buttons or other user processes.
Lastly, it is vital to test all user interfaces, including screens, buttons, touch capabilities, and more.
Why Testing to Fail Fast is Important
Time is a precious resource that you won’t be able to get back in the testing process. As such, it is essential to fail fast so that you can quickly fix any mistakes and get a product out to market on time.
Testing to fail fast can provide as much quality information as a prototype passing a test. If one can more quickly test a product prototype to find where it is failing, that inventor can then begin to innovate and develop a more successful result.
How to Test Your Product
First, it is beneficial to visit a manufacturing facility that builds similar items as the product you wish to market. You should visit a manufacturing plant early in your design phase, as it can help you learn what to do and what to avoid.
There are three key steps to follow when it comes to testing your product:
- Developing a test plan
- Adding test points to your prototype design
- Including an in-system programming interface in your design
You can also manually test each portion or board of the prototype by hand. Likewise, you can produce an automated test fixture for your prototype.
How to Fail Fast
With most technology markets growing more competitive every year, failing fast and becoming efficient at seeking failure can help bring a product more quickly to the market and beat out competitors.
If you want your company and products to stay relevant, you need to outshine your competitors with a product that stands its ground. By failing fast, you can ensure that your product succeeds well before it reaches the market.
Delegating can be the best way to fail fast. As such, every member of your team will need to know their role and the objectives they need to meet to make this happen.
Taking on this attitude can lead your whole team to work faster and troubleshoot any flaws quickly to bring your product to market before your competitors.
Delegating can also allow a team to be more decisive and work together to recognize any failures and take steps to fix the problems.
Failing Fast Produces Innovation
What is learned from failure can also spark innovation. Think of it as failing forward, with every failure, you are closer to creating the perfect product.
Innovation may be about features and new ideas, but it is just as much about finding and fixing flaws or problems within society.
Thomas Edison’s lightbulb was definitely an innovation, but it went through more than 10,000 prototypes before it could be used in the real world.
Failure taught Edison and countless other inventors how to become more innovative. It brought them closer to bringing them to the most useful and failure-proof version of their product.
Final Thoughts
Don’t be scared of failure. Learning to fail fast can guarantee that you achieve a positive outcome for each of your products.
It does not matter how many times your company tests the product, as long as they find a way to make it succeed for the customer.
By designing a product for testing, you can keep your company relevant in an ever-changing industry. Furthermore, you can shorten your product development cycles and increase profits for your company.
Now you can start working on that prototype with fail-fast protocols in mind. It’s time to get started failing so you can get started succeeding!
Written by Daniel Jackson of NI (formerly National Instruments), where they create the tools needed for companies to Engineer Ambitiously™. His current interests are at the intersection of software engineering and DevOps. Outside of work, he is a marathon runner and is working on his first novel.
John,
Great post. The “fail fast” concept extends all the way back to the beginningof the design cycle: how many times could an entrepreneur have discovered that some aspect of his plan was wrong from the very start? These errors of assumption are easy to fix at the start, but expensive to fix at the end.
We discussed this in one of your workshops on TheHardwareAcademy:
Workshop: How to Define and Validate Your Minimum Viable Product (MVP)
Nicely said Dave, thanks for the comment!
On failing:
I couldn’t agree more. Failing is how you discover the boundaries of your design space. In product development, try to force as many failures as possible as early as possible. We learn by examining these failures and figuring out why they occurred. Failing is also to be expected all along the way, although the types of failures will change.
When doing mechanical design, early failures won’t be of the “improper voltage” variety, but a mechanism which breaks under use, or controls that are uncomfortable of difficult to operate. You’ll also uncover problems with assembly (this screw would be easy to insert if only I could climb inside the little box…), serviceability (I can’t get it open without breaking it…), or reliability (worked great the first 37 times…). You can foresee many of these problems in CAD, but not all. Working with a physical prototype always helps.
Finally, it’s important to adopt the proper attitude about development failure, knowing that there will be failures all along the road. Keep telling yourself, “Well, I won’t make THAT mistake again”, and next time you won’t. Always try to extract maximum learning from each prototype cycle, remembering that it IS a cycle. Each cycle is an opportunity to make your product better.
On testing:
Be sure to cast a broad net in your testing. Brainstorm on all of the possible failure modes and important performance requirements, and include a test in your plan that addresses all of them. And perhaps most importantly, get others to try your prototype. Especially those who aren’t a part of the design effort, as they will spot flaws you are blind to.
Very nicely said Bruce, thank you so much for sharing this with everyone!