Episode #14 – 3D Printing and Additive Manufacturing with Steve Szymeczek of Penumbra Engineering
In this episode of the Predictable Designs Podcast I speak with Steve Szymeczek from Penumbra Engineering. Steve is a mechanical engineer that specializes in 3D printing and additive manufacturing.
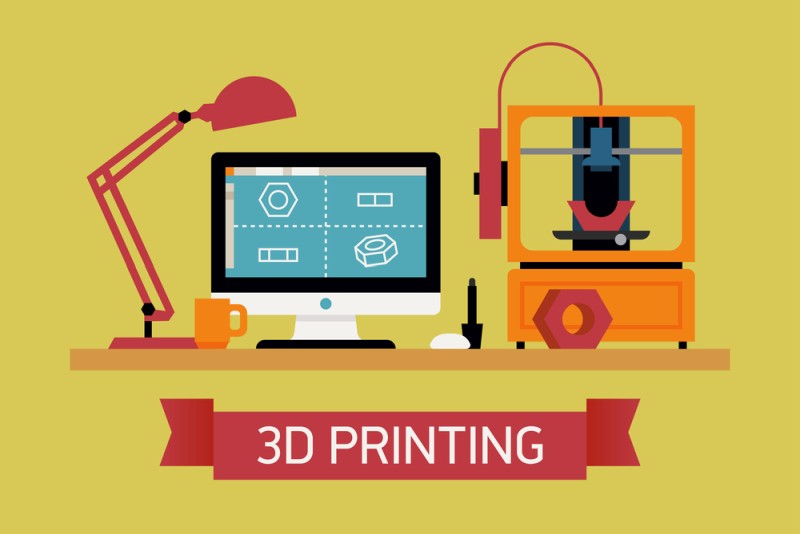
In our call we discuss the pros and cons of additive manufacturing compared to the more traditional injection molding process.
Although many people consider additive manufacturing to be the future of plastics manufacturing, we look at the practical uses now for low to medium levels of production.
Podcast MP3: Download
Subscribe: Apple | Spotify | Google Podcasts | Stitcher
Steve Szymeczek of Penumbra Engineering
Links mentioned in the show:
Penumbra Engineering
Follow Steve on Linkedin
TheHardwareAcademy.com
Podcast Transcript:
John Teel: Welcome to the Predictable Designs podcast, where we discuss all things related to developing, manufacturing, marketing and selling successful new electronic hardware products. I am your host John Teel.
Today I’m speaking with Steve Szymeczek from Penumbra Engineering.
Steve is a mechanical engineer that specializes in 3D printing and additive manufacturing.
In our call we discuss the pros and cons of additive manufacturing compared to the more traditional injection molding process.
Many people consider additive manufacturing to be the future of plastics manufacturing, but we look at the practical use for low volume manufacturing.
Welcome to the show Steve.
Steve Szymeczek: Hey, John. Thanks for having me.
John: Happy to have you on. I think this is going to be a good topic. Additive manufacturing is something I’ve heard a lot about and it’s always seemed like in the pretty distant future that that would be a mainstream method of manufacturing.
I’m excited to meet someone that specializes in this and we can discuss the future of additive manufacturing but also the way that it can be used successfully, the way things are currently already. I think this will be really good.
Can you maybe just start by– I mentioned that you’re a mechanical engineer, you have an engineering firm here in Tucson, Arizona, where I’m located at. If you could maybe just give a quick bio about your background so people know a little bit where you’re coming from.
Steve: Yes, definitely. I grew up in Arizona. I went to Northern Arizona University. I got my mechanical engineering bachelor’s from Northern Arizona University. I went directly into aerospace where I worked initially in aircraft composites and then transitioned over into aircraft interiors, doing designs for airlines such as Emirates.
My last project for that was – you can look it up – it’s the Emirates next-generation first-class. I got my hands on a lot of different mechanical engineering aspects, very highly specialized in computer-aided design.
One of my initials back then was– I didn’t even know what 3D printing was actually until 2013. Stereolithography was something that when I applied for jobs way back when I thought it was some strange weird cryptography type thing.
John: I remember at one point using it and then calling it stereolithography, but not really knowing the term 3D printing at that time. I’m wondering if– As it became more and more [inaudible 00:02:39] I think that’s what– That sounds a little catchier than stereolithography.
Steve: Yes, definitely. It’s inherent to the people that first designed the process. When I did learn about it, I started being really interested. I’d been kind of entrepreneurial wanting to do stuff on the side, and I got the chance in 2014 with a friend from college, we started Penumbra Engineering while I was still working in aerospace and very centric around 3D printing.
Penumbra Engineering, we’re a 3D product development and optimization company. Mechanical engineering design services is our core service. We started out in Tucson with that, working mostly startups and the startup community and Startup Tucson, I don’t know if you’re familiar with them.
We continued to work for aerospace to build up the company and made a lot of good contacts, starting to learn more and more about 3D printing as it progressed from even before we started the company, 2013, up until today, and it has changed drastically just in those seven years.
Back then too when we very first started, I did a lot of talks because a lot of people didn’t actually even know what it was more back then. Today everybody knows what it is. I don’t have to do all the explanation anymore.
John: Although I was going to ask you to explain it.
Steve: I can do that too.
John: I have a very mixed audience, a lot of engineers. Most of those people are going to– Definitely the mechanical will know what additive manufacturing is, but there’s also a lot of nontechnical startup founders and such also that probably don’t know that term. Yes, you want to just jump right in and let’s maybe start by explaining what additive manufacturing is.
Steve: When I very first started back in 2012 basically, the patents that were held by Stratasys and 3D Systems started to fall away. That’s why you saw the rise of it in the last seven to eight years.
The technology that everybody’s familiar with is fused deposition modeling or fused filament fabrication. That’s just the desktop printers that you see around, and that I first started with and owned. They’re very cost-effective. Now, you can get them at Barnes & Noble. They’re very out there in the public, but basically, at its core level, so everybody knows what that one is.
3D printing is basically a process that takes a 3D file, a CAD file, and takes it into a slicing program. It basically slices that into layers. It feeds that into a G-code, which is basically very similar to CNC.
Then through the G-code, it basically traces the outline and the infill of your three-dimensional object onto a build platform. Then layer by layer, it builds that up from the first layer all the way to the top layer. That’s my explanation. That goes–
John: I think that one’s good.
Steve: That translates to most of the technologies. There are actually seven additive manufacturing. There actually might be more now per actually the national standard, so it’s very wide and broad now. It goes all the way from plastics up in the metals and there’s binder jet, and there’s direct metal laser sintering.
At the base level, I work mainly with FDM, fused filament fabrication. Now, the newer technology is the Multi Jet Fusion technology that Hewlett-Packard introduced a few years ago. That one is a little bit different. It’s an industrial-grade system that actually uses elements of binder jet and elements of selective laser sintering.
Just at a very low level, basically, what that means is that this is a powder-based system. It’s a vat of powder, and it’s doing the same layer by layer process that I described. Instead, it is pushing this powder in a z level, and it is pushing a carriage across it and putting thermal energy into it layer by layer, and actually tracing the outline like that. At the end, you’re actually left with a big vat of powder with parts inside and then you pull those out of the powder.
That’s a little bit different than what people are familiar with, but that’s a new industrial-grade type 3D printing and it’s a mixture, like I said, of the two processes called binder jetting and selective laser sintering.
Binder jetting is, when it’s doing that pass, it’s actually putting HP poles and agents down on to the traced outline so that it gets fine details and it’s binding the plastic together while putting thermal energy into it. Then more like a selective laser sintering traditionally, there’s more a point laser which traces that one.
You can see there’s a lot of different technologies. I could go on all day. I’ve done a lot of base-level talks. The main two that I work with are fused deposition modeling, and the Multi Jet Fusion technology, and a little bit of the other technology.
John: Where does stereo lithography fit in? Because that’s different than the–
Steve: Yes. That’s its own category. Basically, stereolithography, I believe was patented in 1986 by Charles Hull, who founded 3D systems. That is basically a vat of resin. If you think I just described the vat of powder, it basically uses the same principles with a vat of resin and a point laser to trace the outline layer by layer. Those are the differences with that.
John: Okay, good explanation. Why is FDM preferred over stereolithography for once you’re doing beyond prototyping and you’re doing manufacturing? It sounds like that’s the preferred technology for manufacturing and not the stereolithography.
Steve: Yes. It’s definitely has shifted probably, like I said, just in the last seven to eight years because the patents fell away and it’s become a lot more cost-effective.
There’s a lot more people in the market. It’s become very flooded, which brings the cost down. Stereolithography is still in essence very expensive just because of the process, and their machines are typically very expensive. There are desktop versions now through Formlabs that are more cost-effective.
There’s actually another category that’s similar to stereolithography, which is the digital light processing, which is a little bit different. There’s a lot of desktop versions of that category now. That is very fine detail for high-level prototyping.
It’s very good for if you need really, really high tolerance, high representation, but it’s UV material which degrades in the sun, so not good for end products or doing any full fidelity testing. Then FDM, through its process, it’s using normal thermoplastics, just like an injection molding. It’s just manufacturing it in a different way.
It’s very cost-effective now. You can get for on the dollar now for material, for FDM. That’s why most people have desktop printers for prototyping. I still do it for low-level prototyping. Then the Multi Jet Fusion has become more cost-effective too.
That’s why we started to use it. You can also use that. I’ll talk about that probably more later, but Multi Jet Fusion’s one of the prototype too, production and technology that’s just started to enter the space in the last few years.
John: Okay, yes, we can get into that here shortly. Ialso have lots of questions about the volumes that you’re capable of doing with these technologies and the cost and everything. Only, I just kind of want to hit on for those listening that didn’t know the term additive manufacturing. You explained it beautifully.
The only thing I was going to add is you mentioned CNC machining. To me, I feel like a lot of people have an easier time understanding subtractive technologies, and then once you understand the subtractive, you understand why 3D printing is called an additive process.
With CNC machining, you just start with a block of plastic, and then you carve away your part like you’re sculpting it out of a block or whatever people sculpt out of, so it’s similar to that process where you’re removing material, you’re subtracting material versus what you described as adding material layer by layers. I just kind of wanted to throw that in for anyone that didn’t still quite understand why it’s called additive technology. Got you.
Steve: It’s one of those things too. I’ve had this debate with many people. Additive manufacturing is the industry standard name. That’s why you hear it’s the legitimate name. I use 3D printing very casually now because more people know that term. They’re one and the same. Additive manufacturing is more related to the industry standard and for the intention of being in end production. That’s another distinction in there also.
John: Absolutely. It’s a critical difference to never confuse prototyping with manufacturing even if it’s the same general process.
Obviously, one of the big advantages is it’s a much smoother transition to go from 3D printing to additive manufacturing because it’s the same basic technology versus going from 3D printing to injection molding. Obviously, it’s a nightmare or it can be a nightmare. It requires a lot of skills and experience to know how to do it correctly that it will work with injection molding, so that’s the big obstacle.
That, and the molds for injection molding are really, really expensive, so I know that’s got to be one of the big advantages to additive manufacturing is you don’t have to have these expensive molds.
Steve: Yes, definitely. Sorry, just to kind of segue backwards here just a little bit.
John: Go for it.
Steve: I left off on my history a little bit. I worked in aerospace all the way up through 2018, and then I transitioned, so I’ve been fulltime with Penumbra Engineering since end of 2017. I made a big push ever since then to become even more additive-centric than we used to be.
We’ve been very much involved in the community, especially in Arizona. One of my other roles is actually the additive manufacturing committee co-chair for the Arizona Technology Council.
John: Yes, I remember seeing that.
Steve: I took on that role a little bit later in 2018, towards the end of 2018. That’s been a very good experience, and I never knew how much 3D printing was in Arizona until I joined that committee and realized that Arizona is a good place to push the technology.
The goal for that committee is to kind of create a hub. There’s lot of industry people involved with that on the aerospace side initially, and now we’ve kind of shifted more towards over the plastic side for Multi Jet Fusion.
It’s just very exciting to see in just the last few years just how much progression is made, and then the cost too. The cost reduction, I think, and we’ll get into it more, has been amazing to me and when it’s decreasing by a factor every year, so it’s very encouraging that it’s going to be more of a player in the future.
John: Yes, I think a lot of people, it can’t happen fast enough to get away from that injection molding, which is like what? 150 years people have been in injection-
Steve: I know, yes.
John: Even longer than that if you get rid of these plastics. Pretty much since I think the invention of plastic, they’ve been injection molding.
Steve: Yes, that’s the thing. 3D printing, a lot of people don’t know. Like I said, it’s been around since 1986. Even partially before that for R&D. It’s been around long enough, and we just haven’t really known about it and it’s starting to get enough progression and it’s getting over the trough of disillusionment and getting more up into the productive area where we can actually use it for what it’s supposed to be used for. I’ll talk about that more, but there is still a very big distinction about when you should use it and when you should not.
John: Yes, I think it’s really exciting to have this coming on onto the scene as a possibility. We’re going to get into the volumes in a bit, but it still doesn’t replace injection molding. At this point, it’s still being used for more like mid-level, low volume production, is that correct?
Steve: Yes. I would say, even though there’s some claims, but I would still say that it is best suited in the low volume manufacturing arena. So you’re not going any more than potentially, maybe up into the tens of thousands of units if you get creative with some product life-cycle costs of total ownership type situations, but you’re really looking at up into a thousand units or so still like the sweet spot.
Past that, you usually look at either bridging to something else or different options for maybe bringing in some other type of value-added product, and maybe it makes more sense. But yes, if you want to start getting into it now, I can start talking about the comparisons and a little bit of the numbers.
John: Yes, absolutely. I said we’re going to talk about it in a minute, but I then went ahead and asked you the questions. We can talk about it now. My only comment quickly is I think it’s really exciting to have a technology, that 1,000 to 10,000 piece price range, obviously our volume range. Once you get up into really high volume, then it’s really hard to beat injection molding for being able to pump out really cheap parts.
But that starting range less than 10,000 units is where a lot of startups especially a lot of companies struggle to manufacture, because injection molding just usually isn’t very cost effective at those beginning numbers, especially if you’re testing out an unknown product and an unknown market and you don’t know for sure if it’s going to be a success, so you don’t want to spend tens of thousands of dollars on those molds. Yes, let’s jump right into anything that you have to share about the numbers and such about additive manufacturing.
Steve: Yes. I’ll go off one of your points there. You made a really good point. I have worked with a lot startups. It varies. We do a little bit in Oil and Gas, a little bit in consumer, a little bit in medical device. We’re pretty diverse, and there’s challenges in all those industries for understanding what at the base level are your materials?
What can you get away with as far as scaling from one up into a certain number? Really, what are your margins too is another question for each of those industries? Usually, the first answer is, you’re in a good spot if you have high margins.
John: Yes, I think most people are doing this to make money if they’re selling a product.
Steve: Yes, I know, probably.
John: You need those margins.
Steve: Yes. We typically work with high margin industry. Consumers are a little bit different. It depends on what it is. That one we play around with a little bit more, but for startups too like you mentioned, it’s critical for them to get into an area where they can scale up into at least a thousand or they can get something out there, they can get feedback and beta production run. It’s super critical in the early stages for them to get to that and to get to that next level of funding.
Most of our testimonials from our customers are, “Yes, we couldn’t have got to the next step without this”. It’s a stage as you know. That’s really one of the core areas that yes, you should look at it for a certain number up to a certain point. I’ll talk through now, what that is, and where are the shades between, there’s a lot of shades? Really–
John: I’m sorry to interrupt, I just want to make one quick point is, because we’re talking about margins. I’ve said this many times on the blog, but it just seems like a good time to reiterate it that you don’t necessarily for most products, making a profit on these first few initial production runs shouldn’t be really a critical goal for you.
If you can sell them at breakeven or even at a small loss, you’re not looking to profit off up for most products, at least consumer electronics, you’re not looking to profit off up when you’re making thousands of units.
Whatever allows you to get those units manufactured for the least amount of upfront cost and allows you to get it on the market as quickly as possible so you can get market feedback, that’s a million hands more important than making a profit off up of this first unit. Anyway, that’s just a slide note there.
Steve: I totally agree because I think it’s the, probably a little bit of the American way, where you go in, and you think you’re going to tow right out the gate, and you’re going to sell 100,000 units. That’s just not- that’s not realistic.
John: That’s probably the American way, but it’s definitely also the entrepreneur way. If you’re not an optimistic person, you’re probably not an entrepreneur. You’ve got to be pretty optimistic be an entrepreneur, so everyone thinks they’re going to sell millions. You may, but it’s just not going to happen nearly as quickly as you think it will.
Steve: Yes. I think definitely for one unit, we’ll start at the base level, one unit, definitely, the best technology to use currently today is to use your desktop printer and start messing around with one unit at a time. That’s probably the most cost-effective that you can do.
You can actually prototype in thermoplastic materials that you could potentially use for injection molding, so to me that’s the best starting point. The secondary and tertiary of those are the Multi Jet Fusion like I mentioned. It is actually fairly competitive almost to FDM in certain areas, even at the one to two in our prototype level.
It really depends on size, so I’ll talk a little bit about that because the size is definitely a lot more of a factor in additive manufacturing than in injection molding. It still is an injection molding, but we’re pretty good at making large tooling because, like you’ve said, it’s been around for so long.
You can get to a good point where you can cover the investment in higher numbers even for a large tool, but in additive manufacturing, the cost is directly tied to the density and the overall volume in the outer extents of the part. Those are the driving factors that you have to think about.
For like an FDM machine, if you’re making one, and I’m sure you probably have one. I’m sure a lot of people listening probably have a desktop printer. A lot of time is spent on that, trying to figure out support materials and you’re trying to figure out how do I print this the best way, and you usually waste a lot of plastic.
It’s good if you’re starting on the very low level, I would suggest mess with that, make sure you understand your initial geometry. That’s how I first started to when we had our couple of printers that it’s very good for that stage.
Now we’re going to go to 5 to 10 units now. Now you’re getting into a little bit of how much you want to bang your head on the wall to mess around with your desktop printer. Maybe you like to do that, but for a Multi Jet Fusion type technology, it is very easy to go from one to five.
Then you actually start getting into where all your residuals for your support material, and all these other things and Multi Jet Fusion technology doesn’t have support material, so you’re not paying for any of that.
As you scale up, and depending on your size, if you’re fairly small, if your parts are very small, it’s very cost-effective up into these 5 to 10 units.
Then as you get into 10 units is where it gets fun because cast urethane, and we had touched on this briefly before this podcast, but cast urethane starts to become competitive and you have to at least consider it when you start getting into that the 10 unit range even up into the 50 unit range, and it really does depend on size.
John: Yes, that’s always my go-to technology that I recommend or suggest is once you get into tens or potentially hundreds of units urethane casting, I hadn’t really considered additive manufacturing because I hadn’t really seen it being used feasibly for anything more than about 10 units.
Steve: Yes, and it’s definitely, I think the one reason that 3D printing does get a bad rap is because the media pushes the, I call it the chotsky, the Yoda head type mentality where it’s not really meant for anything more than just a trinket, so you’ve got to look past that and look at the– I always say go online, look for industry standards. Because that’s, as you know, the industry standards dictate how you will get to the end.
Additive manufacturing is very much an industry-standard now, and in the back end, there’s a lot of standards still being written, but it’s getting there. A lot of my work lately too has been going through and looking for things like UL certification and some of these areas they’re actually have listed now additive manufacturing materials. That just shows you that we’re getting there and the industry is moving. We might not move as fast as I would like or you would like, but it’s getting there.
Going back, I do a lot of cost quoting comparison when I– Like you said, 50 units is like a good sweet spot for interesting because it’s cast urethane and stuff like MJF. They’re very comparable actually in that realm. If you start getting to a larger part, like if you have a larger enclosure, cast urethane will start to make more sense because it’s more into the tooling now.
It’s a silicone mold. It’s a short run mold basically that you’re using and it has a life to it and a number of cycles. You’re basically competing with that cycle of life with how many Multi Jet Fusion parts or a powder vet system that you can fit into a build area.
If you remember back to, I talked about the big powder vet uses, so the economies of scale for that are dictated by how many you can fit into one bill. That you as you know, it’s how long is something running, is the costs. Is one of the main costs. Basically, those are the two you’re playing with, low volume, cast urethane tooling, and how many can you fit into a build.
When you start getting down into smaller parts, and this is where we start getting into some of the value-added stuff where the tip over happens when you need something like a complicated geometry, you need maybe something can be integrated and reduce the number of parts, maybe there’s a value-added component to it that you could do with additive that you couldn’t do with cast urethane. Then that’s when the value-added tradeoff begins. That’ll go up into more numbers as we talk about that and the reasons.
John: One question. Is it not a concern because for most products, ultimately once you get high enough volume, you’re going to be doing injection molding. It seems like it could be risky if your intermediate step is additive technology that you could potentially, you’re going to end up producing something that may not ever be manufacturable using injection molding. Versus your thing casting, it’s obviously a silicone mold but it’s still this similar process to injection molding. What’s your thoughts on that?
Steve: It’s a very good point because I can admit to this, back when we first started, I was not as much into injection molding. I had done some, but you can paint yourself into a corner and then you can be in trouble later. If you have a plan, so you have to have a near term and a longterm.
If originally your value proposition is you are going to make a product and it’s going to be an enclosure and it’s going to be something that is typical to an enclosure design that you’ve seen before, then yes, you want to make sure you have your draft. You want to make sure you reduce your undercuts and all of these elements so that you can. It’s basically the same exact geometry and then you move from cast urethane up into injection molding.
That should always be like you said, and you should always be cognizant that you could do that. I’ll get into this more, but your value is not in the enclosure. It’s in the patent or it’s in the technology of the circuit board. Maybe it has nothing to do with the enclosure, so you should. You should plan. Your core strategy should be to- what you just said and what I just said is you got plan for it. Start here, go to cast urethane, go to injection molding.
John: I guess whatever technology you use for that intermediate step, it all starts with 3D and additive technology for prototyping. That danger is always there. There’s lots of people out there that can design beautiful 3D models that can be 3D printed, but it would take 10 molds and 20 side actions to manufacture it, which would be hundreds of thousands of dollars for those molds probably.
Steve: Yes. I would say you always should play around with it in the beginning to understand least what it is. It’s very good for rapid prototyping. It’s very, very good. That’s what it’s known for. You can make lots of mistakes very quickly and you can continue to make them up to– you get to a point where you start needing to make tens up into hundreds. Then you better really start to be more sure about what you’re going to do.
John: Absolutely. You definitely don’t want to start– Whether you’re doing the 3D model or you’re hiring someone to do it, I think that you need to have at least a fundamental understanding of injection molding so you don’t design yourself into a corner. You don’t have to make your initial 3D model totally ready for injection molding, but you at least have to understand it so that it’s not starting from scratch to transition it to injection molding.
This is actually a course I’m working on right now for my hardware academy that is going to be released later this month. I’m doing a course on 3D modeling for injection molding. In that course, I get into all the great things of wall thickness and undercuts and draft and side actions, and all that fun stuff.
Steve: It’s super important. Because our core is mechanical engineering design services. We still do some design for injection molding. We’ve done even some overmolding design, which is one of the more complicated areas where you’re using two different media, a hard plastic and a saw.
That is an example where we do not have the technology today to do an overmold with 3D printing, or at least it be an end product overmold. That’s a classic example. You should not go down the path to get yourself stuck for something like that.
John: It sounds like if you have a really large product, additive manufacturing is still the best.
Steve: Yes. There are machines that exist out there, but they’re just not very scalable. If you’re doing one-offs, you’ll see a lot of 3D printed plastic statues and these large, they call them big area additive manufacturing, the BAAM machines, where they’ve 3D printed car bodies and all that, but they’ve soon realized that they cannot scale without affecting the project.
John: What would you define as big? You kind of gave some examples. Are we talking more than 12 inches per dimension or? Obviously this depends on the technology and the manufacturing and all that.
Steve: Yes. I know definitely it’s a loaded question. For me, I would say for us, for the technologies that we use as you get up past a cubic foot, so like a foot cube, then you start getting out of that realm of it making sense.
John: That’s an easy number. I think people can remember is one cubic foot.
Steve: There are a lot of methods you can do for something larger than that, but then you start getting into the area outside of the printer. It’s not going to fit on one print. You’ve got to print two and then you got to bond it together and it’s just not scalable. It’s good for prototyping. You can prototype a large object and bond it together, but you’re not going to be able to cost-effectively scale it at all.
John: Okay, good point. Thank you for that. I think I interrupted you at some point. I think you were about to start talking the cost for different technologies.
Steve: Yes. I’ll kind of go. I think I was at cast urethane and 3D printing and playing with those two, but really it’s a term that I hear a lot these days, because it’s additive manufacturing. It’s very hard to make a comparison with just cost per unit. Because really the benefits come from a total cost of product life cycle.
If you’re thinking about going from one to say 10,000 units with additive because you feel like it’s a good option, there’s a good shorthand to do a review if you think that’s good. The first one that I mentioned is complicated geometries. If you have something that has to have ergonomics, something that has non-planar features where, as you know, as you get more complex and shape, the cost for tooling goes up exponentially.
John: Yes.
Steve: Once you start playing that game- an example of one of our products that you can look at was for Perceptive Sensor Technologies, one of our clients. It was an active use case project that was put out through Autodesk. It was a handheld sensor device.
We actually went in and did a lot of ergonomic studies on that. It has a lot of swoopy geometry. It is one of those cases where we looked at it, we measured it, we realized we weren’t going to go up past probably a few hundred units with that one for at that time. It just made sense.
If we try to go out and pursue any of this tooling, we know that it’s just going to be too expensive. This is a startup company. It just doesn’t make sense. That’s number one for making a case for additive, is complication additive is good at.
John: Okay.
Steve: For simplification, probably stick with traditional because yes, like I said, if your value is more in your software and your PCB, you have an enclosure that’s going to go somewhere that it’s a very standard application for just the enclosure, yes, you want to stick with standard. For some of these areas, I’ll touch on it now, that we specialize in, it’s a term called generative design.
It’s a fairly new field, just in the last few years or so. Basically what generative design is at the base level is topology optimization. You may have heard that term before. Basically, in the CAD space, when we go to design, we’re actually looking at alternatives and we’re looking for the best use of material. That ties in very well to additive manufacturing because additive manufacturing can have material literally go anywhere it needs to.
If you know that you’re going to have a complicated geometry, you’re going to be under a certain number of units, we pursue this with our clients. Perceptive Sensor Technologies is a good example where we actually use complicated internal reinforcement structures in a plastic enclosure.
We experimented with that. We were able to get better strength to weight ratio, better overall robustness of the product combined with some of the ergonomic benefits and the fatigue for holding it.
These are the value-added areas that you have to consider, “Are those the things that differentiate your product?” Then, “Are you going to go past a few hundred units or 1000 units?” If not, then yes, it makes perfect sense.
That’s really where additive, right now, is at its best. In the low volume area for these types of value-added complicated geometries and also in the customization area where 3D scanning- you can come in and 3D scans somebody’s body and any interaction ergonomic wise, you can actually have a customized product if you integrate that into the system.
Some of our clients are looking at that because it is, it’s the mass customization model that really the only one that works right now is t-shirts and things with screen printing. Having mass customization in a 3D form is still very new. You’ll start to see it more. You might have seen the Adidas Futurecraft shoes that they tried to launch and then not very successfully.
The goal of that was that mask customized pressure profiles for people’s feet for running, actually create lattice complex geometries suited to that individual. That is a value-added, value proposition, an initial value proposition that you would look at for something similar if you’re looking at using it.
John: Yes, I think that’s a really interesting future that it’s hard to envision all the ways that that could take off in the future as far as being able to customize products.
Steve: Yes. It is, though. The reason why that was not successful was for the reason that economies of scale I don’t think was looked at in total concept product life cycle for that. I can’t be sure. I do know the technology that was behind that one is a technology called Carbon 3D and that’s similar to stereolithography, but it’s more of an industrial-grade version.
John: Maybe in case of sometimes being the first to market isn’t the best. Sometimes it’s better to be the second or third to market.
Steve: Yes, exactly. That’s the hope is that a lot of these first time tries that go into mass market, there’ll be lots of lessons learned and we’ll keep getting there as the standards follow behind.
John: Kind of overall, the additive manufacturing is best for small complex parts that need to be produced at fairly low to medium volume, I guess, depending on what you consider medium, but hundreds of thousands of units.
Steve: Getting into the next stage, if you’re looking at anything more than 10,000 units, let’s say, and you know there’s a chance too that you will not sell 10,000 at a time. As you know, you don’t sell 100,000 units at a time. They’re put on a shelf somewhere, and then they’re gradually sold over time.
One of the advantages that additive also has, because they don’t have the initial costs of the tooling, we actually can level load out through your number of products. If you want to, say, do 50,000 units, and you know your projections look like, “I’m probably only going to sell 10,000 units maybe in the first quarter, I’m going to sell this many,” you only produce as many as you need. It’s a ‘as-needed’ process.
John: There’s not a whole lot of setup time then for it?
Steve: Yes. An example, for the Multi Jet Fusion, it’s literally entire builds worth of parts in 24 hours. It’s literally an on-demand process.
If you think of it like that, there’s no need really to have storage, there’s no need to worry about obsolescence and some of these other things toward the end of the product lifecycle because you’re actually able to produce spare parts basically on-demand and as needed. You can level load so you’re actually not investing. You’re kind of playing into your run rate over time.
John: That can be very powerful, inventory is a big expense for hardware companies, obviously. If you can minimize that inventory you have to have and make it on demand, that’s hugely beneficial.
Steve: Yes. That’s one of the areas that I cross over a little bit. I started there a little bit in the lean startup kind of mentality. You probably know it came from the Toyota Production and there’s a lot of this push-pull system where you only push if you need something, then it actively gets pulled through the system and it gets produced and you’re reducing your waste basically.
Also, another fact too is that a lot of the injection molding is very long term, economically wasteful, and additive is recyclable. You actually recycle that powder unlike the MJF system, so you’re really only using the material that’s absolutely needed to sell a product for the right person.
When you start adding up some of these things, then you can see that maybe you can get away with a few more units, but you have to plan your return on investment, basically more in-depth.
John: That’s always a challenge. It’s always tempting, especially with injection molding or any manufacturing to want to order really large orders because the pricing looks so appealing once you get into– “I could make twice as much money on each unit if I bought 10,000 versus 500,” but that doesn’t hold if you don’t sell those units.
I’ve ran into that with my product where I had too much inventory, then I went back and I needed to make all these design changes, but I had to sell this inventory out first. Being able to make on-demand has lots of benefits, I think.
Steve: I think that basically stops it there. I cannot really tell anybody with any confidence that if you get up into the hundred thousands of units up into the millions of units, you should probably think of injection molding.
John: At least for the foreseeable future, maybe a hundred years from now, we’ll finally get away from injection molding.
Steve: The one thing too that people get uncomfortable especially because injection molding is everywhere, there’s small companies and there’s larger companies, but a lot of the times too, they work in tandem together.
I think right now that’s the good spot where a lot of the injection molding companies are actually investing in additive manufacturing equipment because they realize it’s coming and they want to be able to change their business model in a way that’s most cost-effective and best for their customers.
John: I can see that. I definitely think it’s coming. It’s just a matter of time and when.
Steve: For them, it’s creating a different value-added service for their customer base so that they can do in-house from one to up into hundreds of thousands and everything’s all internalized. The last point too for additive manufacturing, in general, is the notion of distributed manufacturing, I don’t know if you’ve heard this term before. I didn’t really know what it was until about five years ago.
John: I’m not sure. I’ll let you explain it. I’m not sure I’ve heard that term before.
Steve: There’s some different definitions for it. As it applies to additive manufacturing, there is a lot of distributed additive manufacturing suppliers now throughout the United States and throughout the world, and because you don’t need as much infrastructure as you do with injection molding equipment to maintain it, there’s a lot of people that just have one printer now, but a lot of them are industrial printers.
If you think about injection molding, you’re able to pump out as many parts as you can shoot basically in your cycle time. That’s all about cycle time. Whereas in additive manufacturing, yes, it’s about how many you can fit in your build space and how many builds can you get over time, can you pay for that machine’s time, but you’re also not limited to a network of the same printer.
If you think about location and you’re shipping parts to somewhere, the whole notion of having localized distributed manufacturing where you get parts on-demand as needed and they are within a couple of hours from you.
John: That’s huge. I really like that because with injection molding, once you purchase those molds, then the manufacturer is holding onto them. You’re locked into place with that manufacturer, that you may have an agreement where you can transfer the molds, that different molding machines require different molds.
Especially you probably don’t want to ship your molds from China to the US and then back and forth depending on where you need manufacturing. That’s a huge advantage I see that I hadn’t thought of before. It just gives you that flexibility of basically manufacturing anywhere. It’s just a 3D model and a printer.
Steve: Yes. It’s still a little bit in its infancy on that because as you know, the quality aspect actually comes in there too. Is there enough quality across all those printers to get the same part every time?
That’s one of the areas that we’re working a lot is trying to figure out if we want to use a couple of different suppliers to level load some of our work and some for prototyping, some for low volume, are we going to get the same part? Because you know from injection molding, you’re going to get pretty much the same part every time up till the end of life of the tool.
John: Yes. That’s the beauty of injection moldings.
Steve: One of the dangers and the cautions is that if you’re going to use something like a distributed additive manufacturing network, you should be very much more aware of the quality. It is getting there.
Like I said, the standards are getting there. I’m hoping to be more actively involved in some of the standards for some of my other roles because I really think that its place, like I mentioned in our talk, is in this different value-added area that a lot of people don’t think about.
Then there’s a checklist that if you go through, yes, it makes lots of sense. If you don’t check enough boxes, it doesn’t make sense and you should not pursue it. At least it’s an option now. It’s very exciting.
I believe now up and through the next several years, and definitely, we haven’t said it throughout this entire podcast, but the Coronavirus for additive manufacturing has actually been a good thing because our reliance and dependence on overseas has been shaken through all of this.
John: Our dependence on any one location, that’s-
Steve: You’re right, in any one dedicated location, whereas in an additive manufacturing distributed network, it’s really not an issue. It’s more of, are there enough of that one type of technology and is the quality going to be good enough?
John: Interesting. I had not even thought of that. Definitely with the virus, that drives home that importance of having everything distributed.
Steve: I would say, I think a lot of larger companies are realizing this too, because everything I have seen through LinkedIn and just in general, through my network, is that additive manufacturing shouldn’t be an afterthought to an afterthought. It should be your secondary– If you have a main production that is injection molding, high level, high volume, yes, keep doing that, but have options that are viable and understand those options.
John: It’s a great point.
Steve: I think the shifting over this year is going to be additive manufacturing. The one that I can say as an example, and I’ve been slightly involved, is the printing of different masks and ventilators. Really, when we talk about all these on-demand, it’s the perfect model now. It’s basically, can we print enough of them? Are there enough printers of that same type?
John: I started to say a minute ago, if there was ever a time for on-demand manufacturing in the US, it’s now.
Steve: It’s very interesting. It’s going to be just over the next few months. I think it’s even just going to change the face of manufacturing. It’s not going to completely change but it’s going to look very different.
John: I couldn’t agree more. I think there’s a lot of lessons learned right now in a lot of different areas including manufacturing. One last thing I wanted to talk about, you’ve talked about quality.
One of my questions was how does the quality of a production produced through additive manufacturing- how does the quality of that part compare to something that would either be urethane-casted or injection molded as far as both the type of resins that you can use, how those compare to production, then just the appearance, the quality, gloss factors, all those different finishes, can you talk about that and how are those compare to the other technologies?
Steve: Definitely. It’s actually been one of my main focuses lately is in the materials because we are getting to the spot now where some of these standards are actually borrowing some of the same qualification standards from injection molding.
They’re using or trying to use apples for apples. A lot of the time it’s very hard because as I’ve mentioned, the processes, in general, are just very different. One starts off as a powder. The other one starts off as a resin bath.
The other one is basically a roll of filament that is getting extruded layer by layer. They’re all inherently very different and because they’re made differently, they’re just out of there. They come out with different textures and different finishes. I’ll try to describe some of them. It’s very varied and all over the place.
John: Okay. On some of them?
Steve: Definitely for the FDM, I’ll start with that, fused deposition modeling can still be very layer lined, and very much so where it just doesn’t look like an injection molded part because it’s not a smooth machined surface that it was formed up against. Usually, there’s a lot of post-processing if you’re going to use FDM anything past a few prototypes.
John: These are good.
Steve: You can use FDM up into 10s of units and people do it. Even Stratasys has a couple of patented materials that are high performing materials like PEKK, Antero are a couple examples. They’re also actually used for end applications, but there’s not very many of them made and they’re not cosmetic. That just shows you that, yes, for FDM, there’s a lot of post-processing.
There’s entire finishing departments at some of the larger companies dedicated just for finishing FDM parts. I’m not a fan of that.
John: That may be okay for small numbers, but you don’t want to have a lot of post-processing information.
Steve: Yes, definitely. Multi Jet Fusion, on the other hand, because in the technology itself when it’s being formed, as I mentioned, the binder jetting part of it where it’s putting down, in their case, because they’re HP, it’s their proprietary ink that they’re putting down.
There’s actually what they call a detailing agent that is going in and actually outlining the outside and making a finer, smoother finish as it’s printing that layer. This is all done super-fast. I forget, I’m pretty sure the head passes every eight seconds, it’s pretty fast.
That technology, it still comes out grainy. I would say it’s a matte finish that it comes out. Depending on how you run the machine, it can be more grainy and less grainy. It’s definitely a coarse finish.
That one, though, is definitely more acceptable if you’re going for stuff that we work on is a lot of the oil and gas stuff and it’s very much like a matte type finish industry on something that needs to be glossy and you need to consider UV and these other things. You can get away a lot with this matte kind of military look, I call it.
John: It’s not like an iPhone or something where–
Steve: Yes. It’s not going to be a smooth gloss finish. I believe the only technology that gets close is stereolithography, which is not really an end production. You have the Carbon DLS system, which is end product materials that are listed as that. You do have to worry about that technology, is support materials.
John: I haven’t used stereolithography in a while. Back when I was prototyping my part, that was the main technology that was used. The parts definitely did not look production quality. They looked like a prototype.
Steve: You can plan for it. There’s kind of an A surface and a B surface, how you orient your part. If you’re able to orient your part and achieve the A surface on something like the carbon system, it can look very nice and you can get the glossy finish.
That area is probably the closest in that sense, but overall, I would say, there’s definitely more of a post-processing need still with additive, which is more cost. You do have to consider that.
If you have something like you say, an iPhone or some type of electronics where it’s traditionally a very high gloss, or you’re coming out, it looks smooth, it looks clean, it’s very hard to achieve that with additive manufacturing right out of the build.
John: In that case, for something like that, for these volumes, probably urethane casting would be the preferred-
Steve: Yes. Urethane casting definitely gets you closer to what you would equivalently look at for injection molding as you know. Not quite all the way sometimes depending on what it is, but yes, you can get closer. I would say additive manufacturing will continue to get there, but surface finish still is an issue depending on what you’re working on.
John: Excellent. I know for my own product I had started off with stereolithography, but I ended up switching to CNC machining mainly because my product had a lot of snap-fits and things that that was really critical and it was really hard to get those just right using a prototyping resin, I needed the final production ABS plastic.
That’s why I had switched to CNC machining. People listening to this may have heard me tell this story. I’ve mentioned it before, but I had a prototype that had been stereolithography printed and I sent it to- this was Blockbuster Video, they were interested in my product, and I sent it to their lead buyer who had asked for a sample. He gets it. I talk to him on the phone and he just tells me that it’s awkward to use.
I wanted to cry. Eventually, after crying probably for a couple of days, I figured out that what had happened is while mailing it, it had been shipped in the summer, had sat in a UPS truck probably, and it melted just enough to warp it, so it made all the snaps and everything- nothing worked anymore. But it wasn’t just melted like a pile of goo. So it wasn’t obvious to the person.
It’s sort of like walking wounded. To me, I could look at it instantly and tell something had happened to it, but to him, he thought that was the way it operated. Luckily, he knew it was a prototype and he understood what happened. They didn’t have any false illusions it was production quality, so I was able to work past it. Just something to keep an eye out for things like that.
Steve: I think everybody has one of those stories. My story is attempting to print something on a desktop printer and present it to a client and then getting the worst reaction ever because it’s an expectation thing.
Everybody’s very consumer-driven, and even though if we don’t realize it, we have these expectations for things, and 3D printing, like I said, it’s good for a lot of things, but there’s still a barrier to entry where it is, it’s a mental thing.
When you look at something that’s made on a desktop printer on an FTM printer, you see all the layer lines, and you’re just like, “Wow, this looks like it was not made well, and then yes that follows. It’s a stereotype that everything translates to that, and that’s what I try to tell people is, yes, it is true. Your eyes aren’t deceiving you, but there’s a lot more to it than just that.
John: Yes. That’s a common– I think everyone once they start pursuing this path of developing a product, you slowly and sometimes quickly begin to realize how much effort and work goes into all the products that we have in our lives, that there’s a lot of phases that those had to get through or go through to get to the stage that you’re seeing them at, and people just think you can come up with an idea and make a few drawings and send it to a manufacturer and start manufacturing millions of them.
It’s definitely not that easy for sure. I think that’s a really good point. Well, Steve, this has been really insightful. I’ve really enjoyed it. I’ve learned a lot from this conversation. I’m sure the listeners have. Thank you for doing this. I really appreciate it.
If you can tell people how to find you, learn more about what you guys do. Also, I know that you’ve got some courses on 3D printing that you’re working on, if you want to maybe tell people about that.
Steve: Definitely. I’m pretty active on LinkedIn. You can look up my name Steve Szymeczek on LinkedIn, and I’m sure we can put it here in the transcript.
John: Do not guess how to spell the name. You’ll never spell it.
Steve: Yes. Search some crazy weird Polish last name, you might find me. Definitely find me on LinkedIn, you’ll see my name. I’m very active on there. Like, follow. Generally, you’ll see me wandering around commenting on different technologies.
I try to stay very up to date with all the new things going on. If you just generally follow me on LinkedIn and stay connected with me through that, also, you’ll see one of the pages that was launched back in the beginning of February is the 3D Printing Mentality Platform.
That basically, as we’ve talked about in here, one of its main purposes is a barrier to entry. It does talk a little bit about base level 3D printing, what some of the technologies are, but it also is an intermediate where, if you’ve gotten past that point, the tagline is ‘learn, empower, impact’.
We’re putting out a lot of free content and a lot of free article series that talk through some of what I’ve just talked about, and the optimization side of it more in-depth too and generative design, then also on the return on investment. In the next coming months, we’re hoping to put out some free courses.
We are part of a free course up now, it’ll generally get added on to and then eventually we’ll have paid courses too, and that’ll dive deeper into how to develop a 3D printing mentality, and how to take the steps to incorporate it into what you do.
If you find me on LinkedIn, and if I can include it here too, but we basically have a main page for 3D Printing Mentality and we have a blog, I can include that too in the transcript on here.
John: Yes. On the show notes, I’ll have all the links to that here and then your website penumbraengineering.com as well, I’ll have that on there as well.
Steve: All right. Definitely. We’re here to help. I love networking and making connections, not just at the top level and then mechanical engineering design services and planning for 3D printing. That’s our career of expertise. So if anybody has questions or would like to get in touch with me, all my contact information will be on here.
John: Great. Also for any academy members listening, Steve’s in the community, so you could tag in there as well, and he’ll get an email notification.
Steve: All right. Thank you so much, John. This was awesome.
John: Yes. It was great talking with you. This is really insightful, so thanks so much, and stay safe.
Steve: All right. Thank you. You too, stay safe.
John: Okay, that’s it for today. Be sure to tune in next week for another episode of the Predictable Designs podcast.