How to Choose the Production Plastic for Your New Product
Learn about the different properties of plastics, and how to select the best plastic to use for your specific project.
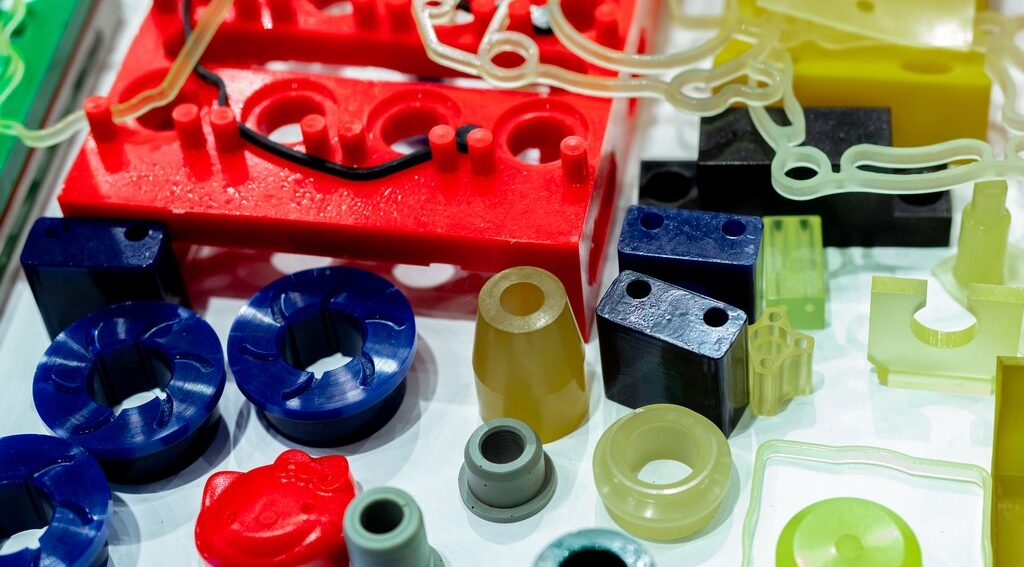
This article is a guest post by Alex Berrou who is a mechanical design engineer, and one of the experts available to help you inside the Hardware Academy.
In any product’s design, there comes a phase when you need to decide on physical manufacturing. Besides the electronics, the main issue that you will encounter is the choice of a manufacturing technology for your product’s enclosure.
Most hardware entrepreneurs are working on small or mid-sized electronic products, for which injection molding will almost always be the technology of choice.
While 3D printing in recent years has progressed into modern manufacturing, it has yet to edge into injection’s core market – large runs of identical items.
Of course, with injection molding being a hundred-billion-dollar market that has been growing for most of a century, the variety of materials on offer is almost unlimited.
Many manufacturers will give you a choice of hundreds of plastics on order. But how do you know which one is best to choose?
In this article, we will go over the most ubiquitous types used, classified in four families of plastics – mass manufacturing, quality, high performance and specialized.
Mass Manufacturing Thermoplastics
These are the most widespread plastics, due mostly to their low cost (1,600 to 1,800 $/ton) and ease of molding. This means that they are the go-to solution for products where volume trumps complexity and quality.
You will commonly see these plastics used to package foodstuffs, large appliances, and home furnishings, for example.
These plastics are notably recognizable by the presence of a three-arrow recyclable logo, with a number inside, that ranges from 1 to 6. These numbers stand for PET, HDPE, PVC, LDPE, PP and PS. PVC, however, is rarely used for injection molded parts due to the emission of toxic fumes.
PET, HDPE, LDPE
Polyethylene terephthalate is unique amongst injection plastics in that its density can be controlled.
High density and low-density variants have their own characteristics, with some commonalities. They are all flexible, resistant to environmental damage, food safe and recyclable.
LDPE variants will be more flexible, while HDPE will be harder. They are, however, not very heat resistant, and don’t take as well to molding as others in these groups. As such, the complexity of the possible shapes that can be molded is more limited.
PP
Polypropylene is, like PET, very flexible and recyclable. The most noticeable characteristic of this plastic is its extreme chemical resistance. It will interact with very few materials and chemicals, which is why it is the go-to solution for glue containers amongst other uses.
This makes it very food safe, as it will not release any toxins into its contents. It is also very injection-friendly, as it will not adhere to the mold.
There is, however, a flip side to this. It is very hard to compound PP with additives such as dyes, and non-specialized paint will not adhere to it. Another negative, it is also flammable.
Polypropylene pellets like these are used to make injection plastic molded parts
PS
Polystyrene is the opposite of PP in many characteristics. This isn’t the expanded foam used in packaging. Molded polystyrene looks like any other plastic at first sight.
However, it keeps some of the same properties: extreme chemical reactivity, which means that it takes very well to additives and dyes, while being light and flexible. It is very easy to manufacture in complex shapes.
This also means that it is very vulnerable to chemical damage. In particular, any petroleum-based compound will dissolve it. The resulting slurry is commonly referred to as “napalm.” Needless to say, it poses a variety of health risks.
Quality Thermoplastics
These plastics are characterized by a higher cost than the mass-manufacturing ones, often in the 2,200 to 3,000 dollars per ton. This is justified by their superior characteristics and means that they are often used for smaller products, for which the cost of tooling trumps material costs.
They are more durable and have better visual renders than the previous plastics on this list. Electronics enclosures are not always made of one of these, but they are by far the most common choices.
You should consider them your default solution, unless your product calls for more specialized materials.
ABS
Acrylonitrile butadiene styrene, thankfully always referred to as ABS, is the best thermoplastic when it comes to appearance, hence why it is used in Lego bricks. Easy and relatively cheap to mold, it excels at rendering fine details and shapes.
It holds vivid colors and complex textures, while remaining light and impact-resistant. Finally, it is a very good electrical insulator, definitely a useful plus for electrical enclosures.
The counterpoint to this is that it does not excel at any type of resistance. It is fairly vulnerable to heat, sunlight, water and other solvents. It burns with a notoriously toxic smoke, so remember that Legos and radiators do not mix.
This 3D pen utilizes coils of ABS plastic to render its creations
PC
Polycarbonate is comparable to ABS in many ways, but it is a harder, more environmentally resistant material. Its aesthetic qualities are also quite good, and it has the added advantage of potentially being transparent.
On the other hand, it is more brittle and prone to scratching than ABS, while being one of the least food-safe plastics available.
ABS/PC
The most widely used solution for the manufacturing of small and medium plastic enclosures is to blend ABS and PC in varying proportions.
Picture it like a slider. At one end is the lightness, cheapness, impact resistance and visual properties of ABS. At the other end is the hardness and environmental resistance of PC.
The proportions of each plastic used will determine the final properties of the mix, allowing for a fine-tuning of the process depending on the use cases of the product.
Of note, all of these blends will share the common defect of ABS and PC – a vulnerability to a variety of chemicals and solvents.
High Performance Thermoplastics
These plastics are the kind used for highly technical situations. They are very costly.
POM costs $3,000/ton and Nylon is a whopping $5,200/ton. They are also very hard to manufacture. Their selling points are mechanical properties designed for extreme environments and applications.
Polyamide, commonly known under the brand name Nylon, is a highly durable, heat resistant, electrically insulating plastic. It is particularly noted for its resistance to friction, which means that it can be used to make gears and mechanisms with properties close to some metals. Additives can easily make it fireproof.
It is also, however, possibly the hardest material to injection mold. That is in large part due to its tendency to absorb water. Nylon must absolutely be stored and formed in a zero-humidity environment.
It reacts poorly to injection molding and must be injected at high temperatures and pressures. All of this on top of its eye watering material cost means that Nylon is seldom used for large components.
POM
Polyoxymethylene, also known as acetal, is a very crystalline thermoplastic. That means that its molecules solidify into an organized matrix instead of a shapeless mass.
In turn, this makes it extremely hard. In terms of texture, the finished product can be mistaken for polished stone.
On top of its hardness, POM is very heat and chemical resistant. This makes it very popular for military, sports, and construction applications, and for fine parts that might otherwise be fragile, like eyeglasses.
The main difficulty of POM is in its manufacturing, it is in fact rarely injection molded. It is more commonly extruded as slabs, which are then machined into parts. Furthermore, with very low plasticity, POM can be vulnerable to cracking and scratching.
Specialized Thermoplastics
Sometimes, rarer properties are required for an enclosure. All of the plastics that we have listed above are fairly rigid, and those that can be made translucent are not always ideal.
This is why some more specialized plastics and blends have been developed that carry these properties.
TPE
Thermoplastic elastomers are a diverse family of plastics that share some properties. They are highly elastic, but nonetheless behave like thermoplastics in that they become soft then liquid at high temperatures. This means that they can be injection molded like other thermoplastics.
Behaving like rubber, these tend to be recyclable and easy to mold. They are widely used for purposes such as gaskets, shoe soles, medical equipment and such.
However, TPEs tend to be vulnerable to high temperatures, which will cause them to lose their consistency and break easily. At $3,500/ton, they are also rather costly.
TPU
Thermoplastic polyurethane is a subset of TPE, which is harder and more resistant to heat and chemicals. If TPEs behave like rubber bands, TPU behaves more like car tires.
This increased toughness means that they are commonly used in high-end enclosures that are often over-molded. That is when something is molded on top of an existing part while it is still in its own mold, in order to create flexible buttons, gaskets etc.
TPU is slightly costlier than TPE, and somewhat harder to inject. The main difference between the two is their degree of elasticity.
Most plastics can be dyed any color, like these acrylic tubes
PMMA
Poly (methyl methacrylate), more commonly referred to as acrylic, is a transparent thermoplastic.
Unlike others on this list, its transparency is comparable to that of glass. In fact, it shares most of its properties with glass. It is very resistant to chemicals, food safe, and keeps vivid colors when dyed.
This makes it popular for a variety of transparent parts, either as part of another product (inserted into an enclosure, say) or in sheets.
The defects of acrylic are also comparable to those of glass. It is prone to scratching and cracking under stress, unlike less rigid materials which will bend. Its heat resistance is also sub-par.
Let’s Now Pick Your Plastic
Now, let’s answer the question that we posed at the beginning of this article. What should the material for your enclosure be?
Your product is probably not disposable, nor very large. These are seldom the case, but let’s nonetheless look at them.
The larger the object, the more critical the price of the material: hence the mass-manufacturing ones. PET is always a solid choice in such circumstances, with LDPE for lighter and more flexible parts and HDPE for heavier and tougher ones.
If exposure to the elements in general, and chemicals in particular, is a major issue then choose PP. If exposure isn’t much of an issue, then go with PS.
For smaller products, where the quality of the finish is critical and the price of the material less so, ABS and PC should be your go-to materials. ABS is prettier, lighter, cheaper, more flexible and blocks electricity.
PC is harder and more resistant to the environment. Blending the two in various proportions will give you the best of both characteristics.
The high-performance thermoplastics will seldom concern you, unless you are designing high-end parts for automobiles or aeronautics.
If so, remember that POM is reminiscent of polished stone in behavior, that Nylon is resistant to everything but chemical attacks, and that both are very costly to manufacture.
Finally, for specialized purposes, PMMA will give you the best transparency at the cost of being easily scratched, while TPE will have the texture of a rubber band and TPU that of a car tire.
This is, of course, a simplified overview. As I have mentioned, the size and age of the injection molding industry cannot be overstated, and the amount of effort and research that have gone into the field are to scale.
This means that technologies, materials and procedures are hugely varied, with most manufacturers having their own equipment, suppliers and habits. Always consult your manufacturer and obtain their opinion before commencing any manufacturing, as they will know best what works in their layout.
In particular, for every characteristic of every plastic that I have listed here, you will find some sort of additive or methodology that puts the lie to it.
There exist waterproof Nylons, heat resistant ABSs, and PETs that look better than either. Everything is possible with the right chemistry.
Essentially, you can picture this list as an off-the-shelf solution. The plastics on this list are widely available, and appropriate for most of your needs.
But major companies with lots of resources will almost always design their own proprietary blends of plastic to match their specific needs.
I think you’ve underestimated polycarbonates in your summary. I remember when GE introduced Lexan in the mid-sixties. They gave away clear discs (about 4″ dia x 3/16″ thick) and invited recipients to try to break or dent it. Even clamping it it a vise and hitting it hard with a sledge-hammer wouldn’t crack it – only a dent. In fact, it’s so rugged that many car bumpers are made of it. And optical-grade polycarbonate is used to make compact discs. When I worked at Capitol Records, I watched the molding process, which was quite similar to the process of making vinyl LP records – and, of course, the CD requires exquisite detail to replicate microscopic detail from the metal “master” disc in the mold. Lexan would be my first choice for an electronic enclosure for a portable product subject to physical abuse.