Low-Volume Manufacturing Methods for Custom Plastic Parts
Discover which method is best for low-volume manufacturing of custom shaped plastic parts (typically a product enclosure): 3D printing, urethane casting, or injection molding.
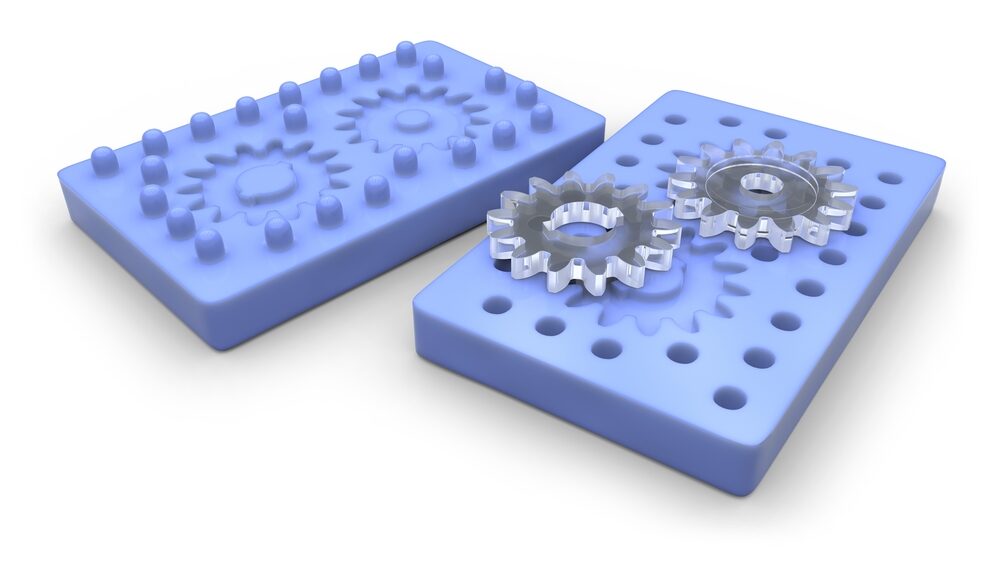
This article is a guest post by Alex Berrou who is a mechanical design engineer, and one of the experts available to help you inside the Hardware Academy.
Once you have finished the design of a mechanical part, or ideally before, you must start to think about how it will be manufactured. This can have a considerable impact on the 3D design itself.
Although the final method of manufacturing for higher volumes will generally be some form of injection molding, there will most likely be a need for an intermediary process as you validate your product and ramp up production.
A product’s shape and functions often evolves early on, and you do not want to invest too much into the production of a non-validated concept.
Hence, the need for low-volume manufacturing methods. These methods can range from making a single prototype to producing several thousand units, but they all have in common that their setup cost is minimized in order to allow for more flexibility.
In this article I will present the three most common technologies used to manufacture new products in smaller batches: 3D printing (of two sorts), urethane casting and injection molding.
FDM 3D Printing
Process
The process for FDM is a familiar one to many hobbyists today. A plastic filament is heated and pushed through a thin print head, which deposits the results in successive layers on a print bed.
This is one of the most flexible manufacturing methods available today.
The immense diversity of machines and materials available means that a wide variety of results can be obtained. But the principle always remains the same, with different brands only changing the mechanical solutions involved.
Printing a part will take anywhere from a few minutes to days. Count on it taking roughly one hour per cubic inch with average settings.
Results
The quality of results obtained by FDM vary widely depending upon the appropriateness of the design.
A part that is well-designed for FDM will look quite good, like this green part pictured below.
A part that does not follow the long list of requirements will be considerably less attractive, like the following:
In all cases, the final appearance of an FDM printed part is always layered, due to the technology involved.
Advantages
The main advantage of FDM 3D printing is its ubiquity. With 3D printers being cheap and accessible, you are liable to find one near you anywhere in the world.
This in turn means that the cost of production will be very low, and the delay between iterations will be very short.
Thus, you can afford to order individual parts quickly, test them, refine the model and have them printed again without wasting too much time and money.
In addition to this, a well-designed FDM printed part can be extremely solid, and the variety of filaments available means that you can always find one that fits your needs.
Disadvantages
The main issue with FDM printing is its inaccuracy (generally 0.5mm) and layered appearance, which means that these parts will almost never be valid for commercial purposes.
They simply do not have a nice, polished appearance, and will turn many customers off even when correctly designed.
Furthermore, their anisotropic nature means that they react differently to forces in different directions. This can impose some limitations.
For instance, it is almost impossible to design an enclosure that closes via snaps because they will break off due to the fragility of the plastic.
An ill-designed FDM part will be extremely fragile. Additionally, since the filaments used in FDM are explicitly designed to melt easily, they do not take well to heat. PLA will deform in temperatures as low as 70°C, while the best nylon will not resist 130°.
Note from John Teel: I actually had a FDM prototype of my own product partially melt while in route to an important retail buyer who had requested a sample. So be very careful about shipping FDM units during hot weather.
In terms of price, while the absence of a setup cost is an advantage, the per-part price of FDM printed parts can quickly add up for larger runs, as there are few economies of scale to be had.
Ideal Uses
FDM is best used for rapid, non-commercial prototyping. For a low cost, it allows you to very quickly get feedback on the feasibility of your designs.
You can use these prototypes to demonstrate how your product works, but you will probably not want to actually sell them.
SLS 3D Printing
Process
SLS printing is a more advanced process than FDM printing.
SLS printers (and MJF which is a close cousin) use a laser to melt, or sinter, a bed of plastic powder. Once a layer is made solid, the bed will lower a notch, a new layer of powder will be added, and it can be sintered in turn. Printing time is comparable to FDM (approximately one hour per cubic inch).
This process has been developing very quickly in the past few years, and may be set to overtake FDM as the most used 3D printer by professionals.
Variants can also print metals, and are increasingly used in the aerospace industry to make shapes that would otherwise be impossible to obtain via other technologies.
Results
The results of SLS are nice and professional-looking, compared to FDM. The dimensional accuracy is much better at roughly 0.1mm, and there is no layering effect.
The results always feel a bit granular, though, unlike the smooth finish of molded parts.
Quality for an FDM printed part versus one printed with SLS.
Advantages
SLS parts shine in comparison to FDM, while having most of the same advantages. Though roughly twice as costly they remain affordable in small quantities, and are increasingly available everywhere. If you can’t find a vendor in your city, there are online vendors that offer these services.
The quality of SLS parts is better than that of FDM. They do not have the layered appearance, and are thus more beautiful and more resistant. The default material used is nylon, meaning that temperature resistance is noticeably better.
SLS is one of the most adaptable technologies in terms of shape, and will print almost anything. This is because the powder acts like a support even for overhanging parts, unlike FDM which requires specifically printed support structures.
Disadvantages
The disadvantages of SLS printing are similar to those of FDM. The finish, while homogeneous, is not completely smooth, and this may be an issue for some applications.
The per-part price, which is higher than FDM, quickly accumulates with the number of models printed. And the fact that the only material commonly used is nylon means that SLS printed parts can be vulnerable to certain forms of chemical corrosion.
Ideal Uses
SLS, unlike FDM, is a commercially viable technology. SLS is great for very small runs of products, up to 500, or printing unique models. Like FDM, SLS has a very short lead time for getting parts.
Urethane Casting
Resin casting process using a one-face silicone mold.
Process
Resin casting, commonly known as urethane casting since urethane is the most common type of resin used, is a rather complex, multi-step process compared to 3D printing.
The first step involves making an original version of the final shape. This can be achieved by 3D printing, sculpting, using a pre-existing part, or a variety of other solutions.
Once the model is complete, it is covered in silicone in order to create a mold. The complexity of this step can vary depending on the number of faces that must be recreated.
Once this silicone mold is complete, it can in turn be used to cast any other chemically-bonded material. This will generally be urethane resin, but can be a variety of others, including more silicone.
This will take several hours, after which the part can be removed and the mold reused a few dozen times.
Some manufacturers will put their molds in a centrifuge, in order to get smaller details and faster solidifying times.
Examples of two-faced silicone molds.
Results
The results you get with resin casting are comparable in quality to injection molding. Properly designed, the level of detail can be extreme and the smoothness irreproachable.
Examples of urethane casted parts made using a silicone mold.
Advantages
The main advantage of resin casting is the excellent surface quality of the results, which is one of the only ways to obtain perfectly smooth parts without tedious post-treatment or expensive injection molding.
Furthermore, their mechanical properties are very good, and can rival injection molded parts in many cases.
There are two things that castings can do that are not possible with 3D printing.
Casting is very flexible in terms of the types of materials that you can use. This means you can produce flexible or transparent parts. You can also choose from a wide variety of transparent resins and flexible silicones.
Parts made with 3D printers will be stiffer, at best rubbery like a tire. 3D printing can be slightly translucent, but not transparent, due to their layered composition. In contrast, there is a wide variety of transparent resins and flexible silicones that can be used with silicone molds.
Resin casting is furthermore a very flexible technology, as the silicon molds will deform easily, which greatly simplifies part removal compared to injection molding.
Disadvantages
The main negative of resin casting is it’s a more expensive solution than 3D printing. Due to the manpower-heavy nature of the process, both setup and per-part prices can be high.
It is cheaper than injection molding, but more expensive than 3D printing.
Also, the basic resins tend to be very hard and prone to shattering on impact. However, this can be alleviated by using different materials.
Ideal Uses
Casting works well if you need to produce small runs of 100-1,000 parts. Smaller runs can be worthwhile if specific conditions, such as transparency, flexibility, smoothness or heat resistance, are necessary.
Larger runs can work well for parts that are too complex in shape for injection molding.
Injection Molding
Process
The process of injection molding is nominally simple, though the technology is anything but simple. It basically consists of squeezing melted plastic into a mold, then waiting for it to solidify.
Where it gets complicated is in the machinery that is needed. Injection presses are multi-million dollar setups, with molds costing in the thousands each.
A very large screw will heat and mix plastic granules in order to obtain the injection material, which must then be forced into the mold with extreme pressure so as to fill it before it hardens.
Due to this high pressure, the molds have to be held closed with considerable force. Then they must be cooled so as not to overheat and in order to control the solidification of the plastic.
Finally they must eject the parts by opening the molds, which can be a complex process since the molds are made of solid metal and are not at all flexible like with a silicone mold.
Injection molding for low-volume manufacturing uses aluminum molds. This reduces the initial cost and mold production time compared to steel molds, but it also reduces the mold lifetime since aluminum is softer than steel.
Simple basics of producing an injection molded part.
Results
The results of injection molding are generally very high quality, though they depend on the quality of the mold. The more carefully a mold is machined, the better the result, but that takes longer and comes with a higher price.
Example of an injection mold and the resulting part produced.
Advantages
The low, per-part price of injection molded plastic is the reason why it dominates manufacturing. Parts can be made for a fraction of the cost of the other technologies on this list, often for only a few cents each.
The appearance and mechanical properties of injection-molded parts are also top-tier, though they will not always take very well to heat depending on the plastic used.
Disadvantages
The main issue with injection molding is, of course, the high initial mold cost. Manufacturing a mold, often called tooling, and setting up everything for production is costly and takes a significant amount of time.
Example of an injection molding machine.
While molds have very long lifetimes (thousands of cycles for aluminum, nearly unlimited for steel), this means that manufacturers will always demand a very high price before commencing production.
Generally, you can plan on spending several thousand or tens of thousands of dollars before you begin production with injection molding.
Also, the mechanical constraints of injecting the plastic and then extracting the part mean that designing a part for injection molding is a very complicated process, requiring expertise in the field.
The limitations imposed on the designer are even more extreme than they are for FDM printing, and strongly limit the shapes that are feasible.
It is very common for inexperienced developers to design a part that can be 3D printed, but that can never be injection molded without major redesign.
Ideal uses
Low-volume injection molding can be worthwhile for mid-sized runs, in the thousands of units or more.
For runs in the low thousands you can make your mold using a softer, and hence cheaper, metal like aluminum. Aluminum molds are significantly cheaper because they are quicker and easier to create due to the softer metal.
Aluminum molds work well in low volumes, but for higher volumes you will need to migrate to steel molds which are more expensive, but much more durable.
Conclusion
The table below compares the merits of resin casting versus injection molding. As you can see, casting mainly shines through with its lower setup cost and simplification due to the flexible nature of silicone molds.
Injection molding has the big advantage of low per-part cost. Other properties are overall equivalent.
The graph below highlights the general balance of value for the three technologies.
For very small runs, below a hundred or so units, 3D printing can be a good option. It can also be worthwhile in larger quantities if a very quick lead time and product design flexibility are important.
For small runs, from 100 to 1000, urethane casting is usually the best option. It can also be worthwhile in smaller quantities if factors such as transparency, flexibility, smoothness or heat resistance are critical, since 3D printing does not offer them.
Casting can also be worthwhile in even larger quantities if the shapes are too complex for injection molding.
For medium-volume runs, in the 500 to thousands of units range, low-volume injection molding will lower your per part production cost significantly, and is generally the preferred technology.
That was a nice high-level introduction, thanks. Although I would echo the comments about defining your acronyms before use, and also point out that your embedded YouTube videos seem to have been swapped.
Good explainer as far as it goes, but the universe of 3D printing is wider. See: https://www.thomasnet.com/articles/custom-manufacturing-fabricating/types-of-3d-printing/
For a good rundown of a bunch of technologies
Thanks Bruce for the feedback and for sharing that article!
Another solid article…concise and saturated with highly relevant info. Keep up the good work guys!
Great to hear, thank you Josh for the comment!
Just a suggestion, you should define your acronyms before you start throwing them around. SLS, FDM, PLA? Otherwise a very informative article. Thanks
Thanks for the feedback, and good point on the acronyms which normally we try to be good about defining. I’ll probably go back and add them to this article. Thanks again!