How to Avoid Common Mistakes Developing and Manufacturing Your First Hardware Product
Learn first hand from the experiences of two other companies bringing their first hardware product to market. One product is a Bluetooth wearable, and the other is a smart home product.
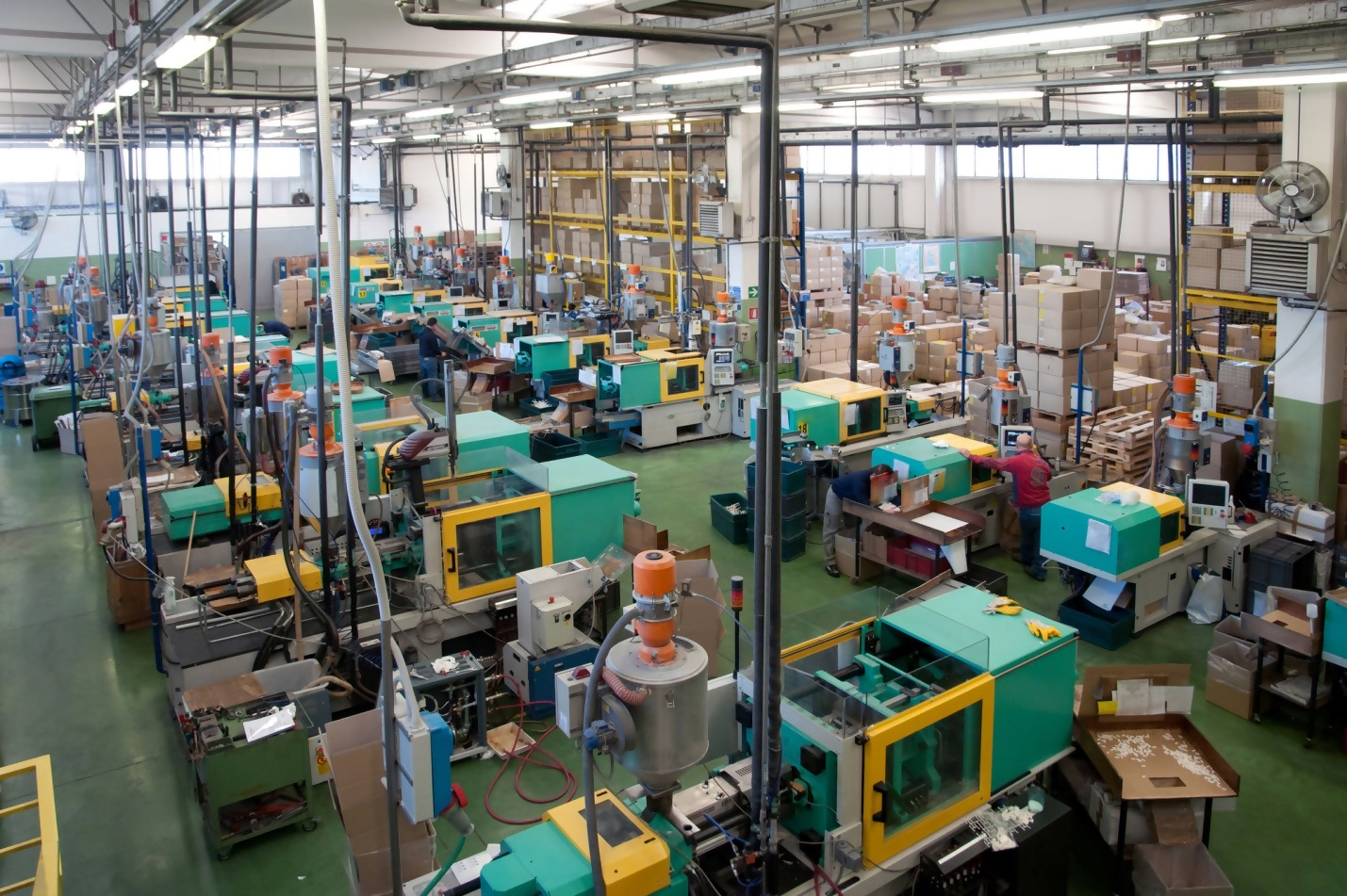
My name is Dave Millman and I help high-tech startups find their first customers. John Teel asked me to share some of my first-hand experiences so as to help you avoid many of the first timer manufacturing mistakes.
During the past couple of years, two of our clients who were both new to manufacturing have launched their hardware products.
One product is a Bluetooth wearable device with two PCBs and three SKUs (Stock Keeping Unit is a number assigned to a product for inventory tracking). The other product is a smart home product line with four PCBs and a lot of SKUs.
During the design and manufacturing preparation, these two hardware startups made multiple design and manufacturing mistakes. They were also stung by a number of partner “surprises”.
This blog post summarizes the mistakes that ultimately cost them time, money or both. Hopefully this will help you avoid making some of the same mistakes.
Design Tradeoffs
The three biggest design mistakes are:
- Offering costly features that nobody wants. The startup with the Bluetooth wearable product lost four months because of design and supply delays for a premium feature. This feature contributed just a small percentage of their crowdfunding volume and almost none of their follow-on ecommerce sales.
- Critical features are missing.Many companies fail to test the “whole product” with customers, thus they miss a key feature that slows their startup’s growth. The most common missing features are APIs to your product, integrations to other APIs, and emerging communication protocols.For example, the wearable company created Android and iOS apps, but did not provide data interfaces to other fitness apps or products.
- Building what you could buy cheaper. Many product categories are already in production at high volume and low cost. If you need that functionality as part of your product, it may be cheaper and faster to buy an existing product/module/subsystem/IP and build your value on top of that. Or, get to market faster by using an open source software platform that you can upgrade later.
Compliance & Certifications
Both of the products we’re discussing utilized wireless radios, so both required testing and certifications across many countries worldwide.
- Don’t underestimate compliance effort: Compliance with North American, European and Asian regulatory requirements for power and RF products takes time, even if you are relying on pre-approved RF modules. For example, your manuals and packages will all need region-specific declarations, symbols, etc.
- Some countries require documentation and labeling in their native language. For example, Canada has very strict requirements that both English and French are included on the packaging. They even require each language to have the same font size.
- Do not assume that you can sell a product that performs the same functions as a product on Amazon. Many products at Amazon do not actually have the certifications they claim on the package. Others do not meet safety, emissions or other regulatory requirements in many jurisdictions.This takes a lot of research to get right. If a product is discovered to be non-compliant, an overseas manufacturer will just dump their inventory in another country and run. You probably can’t do that.
- The fact that a product is available on Alibaba says nothing about whether that product is legal in any country, including China. Be sure to ask for certification documentation.
- RF modules: Available RF bands in Country 1 may not be available in Country 2, no matter what your supplier tells you. Transmit power limits vary country by country as well.
- Products that communicate data need security designed in from the beginning. This one will really hurt if a user complains that PMI (Private Medical Information) such as pulse rate or body temp is not securely transmitted and stored.
Enclosures, Plastics and Injection Molding
- Injection molded parts look and feel different than 3D printed parts, even if they use the same material.
- Do not approve injection molded parts for volume production until you have tested everything, especially assembly. Different materials behave differently, and different colors may also behave differently. Since there is little quality control on bulk plastic supplies, different lots of the same plastic may exhibit different colors, textures and manufacturing characteristics.
- The ultimate failure is when the pieces of your final product do not snap together properly, or break during assembly, because one or more materials changed during the run-up to volume production.The more injection molded pieces you need to assemble together for your product, the more trouble you may experience in assembly. Subtle things, like different plastics bending or snapping together differently, have plagued injection molded parts since the early days of injection molding.
- Faceplates and touch panels are the hardest to get right.
Batteries & Charging
- Just because your energy source has 2000 mAh capacity does not mean you have 2000 mAh to work with.
- You need an in-depth understanding of the discharge characteristics of your chosen battery. They do not produce steady voltage/current over a discharge cycle, and this power profile changes as the batteries age.
- If you are recharging, you need an in-depth understanding of the charge characteristics.
- “Boost converters,” components that convert a battery voltage to a higher voltage, may be only 20%-50% efficient at some operating points. This means half or more of your battery power goes to heat (beyond just the self heating of the battery).
Supply Chain and the BoM:
- Check availability of your BoM continuously, especially if you experience delays. A common part last from year may hit its end of life this year.
- Changing just one component may require re-testing for compliance.
- A single different component can cause your device to fail emissions testing.
- The only constant about component lead times is that they change continuously.
- As you experience design delays, confirm your schedule with your other vendors. If you slip your schedule toward the end of the year, some vendors may not be able to accommodate you.
Reliability Testing
- Do not skip or shortcut any accelerated aging or load testing.
- Ask yourself, “Once my wonderful widget has been dissipating power for 2 years, what’s going to change in its appearance/performance?” This is crucial for anything that connects to line power, especially if installed within an enclosure with poor cooling.
- You need to understand the aging characteristics of parts that rotate or parts that enclose rotating parts. It’s no fun when, a year after you start shipping, your Amazon reviews all start to say, “It worked great for a few months, then the fan started clicking, then it quit altogether.”
Vendors Coming Out of the Woodwork
- If you achieve any notoriety (crowdfunding, trade show booth, magazine article), vendors will show up out of nowhere offering to help you. Beware!
- When an unknown vendor shows up offering a cheaper/faster/better alternative to a name-brand component or process, you must evaluate every possible risk factor. Do not let the fact that one spec is better blind you to potential quality/reliability/supply problems.
- It is extremely tempting to buy a “better” component (higher power RF module, better display, nicer retail package, etc.) to differentiate yourself from the competition.A differentiated feature helps you only when customers care enough to pay more for it. Arbitrarily adding better components will give you a fast and costly lesson in consumer product economics. Go back and compare your very first BoM estimates with what you actually ship. You may cry.
- With the rise of crowdfunding, a whole ecosystem of outsourcing vendors has emerged to handle everything from industrial design, manufacturing preparation, overseas manufacturing, testing, packaging, shipping and fulfillment.Some of these vendors are quite good and will make your life much easier. Some are inexperienced and/or incompetent. Some are semi-legit but prey on newbies. So use caution when selecting your vendors.
Tricks Vendors May Try on First Timers
- Swapping parts for cheaper parts (everything from capacitors to microprocessors to batteries)
- Substituting lower quality plastics, or less costly finishing steps (paint, polish, etc.)
- Substituting lower quality PCB materials/thicknesses/tolerances.
- Substituting non-compliant RF components
- Substituting entire factories, production lines or staff for the ones they showed you on tour, before that big celebratory dinner.
- Beware of unlabeled components. Especially be cautious of components that have had their identification removed (rubbed off/painted over/labeled over/ground off).
- When you submit a design one day late, they may tell you that will cause a 3-month delay. After many late night negotiating sessions, they will relent and revert to the original schedule after you pay a cost increase of 20%.
- Bad supply partners play time against you, again and again. They know you are in a rush. They aren’t. (This also applies to investors.)
- Watch out for vendors claiming a capability you need, and offering a drastically lower price. You need to visit their actual production facility, confirm that their name is on the door, and watch them do that thing. Literally thousands of manufacturers come and go every year in Asia.
- Yes, unscrupulous vendors will put your product at risk to pocket an extra $1,000.
Timing, Shipping & Logistics
Remember how naive your original schedule estimate was? If not, you will discover this soon enough.
These factors will further impact your schedule as you get closer to shipping product:
- Factories are very busy from July to December ramping up for the Christmas holiday. Pricing, scheduling and everything else is more favorable from January through June.
- Finishing your schematics and simulations in July does not mean you have plenty of time before Christmas!
- Software takes more time than you think. In fact, everything takes more time than you think.
- In late 2019, many hardware startups are learning that their landed cost will be 25% or more higher because of the US-China trade war and tariffs. This will kill some companies. This changes daily so be sure to monitor these tariffs closely.
- You need to know the landed cost in the distribution country. Evaluate every option including using different shipping vendors in each region (Americas, Europe, Asia)
- Deciding to use air freight to get the product here sooner has flipped more products from profit to loss than any other single factor.
- Sales tax, VAT and shipping costs flummox everyone. Some customers in some countries will get hit by shipping and VAT that exceeds their purchase cost.
- Online stores (Shopify, Etsy) are notorious for miscalculating VAT and shipping costs outside the U.S. because of the number of variables (weight, shipper, country, taxes). This is further complicated by the interface to a third-party logistics partner. Amazon seems to eliminate much of this risk, at higher cost to you of course.
Avoid “First Timer” Mistakes
You can avoid most of the mistakes above by following these guidelines:
- Recognize that every engineering decision is an imperfect tradeoff of multiple factors including price, performance, reliability, size, power, delivery and more. Don’t reduce decisions down to a single factor, such as “this one is cheaper.”An experienced engineer would say “this one is 2 cents cheaper and available sooner, but consumes an extra 2mW and will require a board spin because the pinout is different. Also the vendor hasn’t responded to my request for reliability data.”
- John Teel’s recommendation to hire a different engineer or consulting firm to perform a design review (or join the Hardware Academy for design feedback) will help you avoid many of these problems. Most established companies have a formal and rigorous design review process for this reason.
- Test your assumptions with customers early and often. Invite customers to meet the whole team, talk about their problems and critique your solution.
- No hardware startup ever said, “the time we spent checking references was a waste.” This means separate reference checking on every vendor, even if they were recommended by a trusted partner.
Horror Stories
All of the problems above are real. Even the most experienced manufacturers get stung from time to time. Here are some recent examples:
- Samsung Galaxy Note 7 smartphone catches on fire
- SEC hits failed Apple sapphire glass manufacturer with fraud charges
- China Factory Scams: Their Time is Ripe
- Reddit: Overseas manufacturing horror stories
Conclusion
Developing and manufacturing a new hardware product is a process littered with numerous obstacles. Avoiding these obstacles will save you time, money or both.
Try to identify any obstacles as early as possible. Seek advice from those that have dealt with them before, and formulate an upfront plan to either avoid them entirely, or surpass them.
Regardless of how much planning you do, or how much experience you have, unexpected problems will always come up. But you can succeed if you are adaptable and persistent enough to push through these problems whenever they arise.
NOTE: This is a guest blog by Dave Millman of BizDev.Global. Dave helps high-tech startups find their first customers, from market validation through technology partnerships into high volume manufacturing and sales. Dave is also one of the many experts available to help you inside the Hardware Academy.
This is a great list. I confirm many of these issues do come up a lot.
The only point I am not sure about is about asking for references for every vendor. Imagine you are a good manufacturer, doing a good job for 10 customers. And you have people contacting you every day, and asking for references. The 10 customers won’t want to be emailed/called constantly. It just doesn’t work.
Good point, thanks for the comment Renaud!
Thanks for the PDF version which I have printed off and stuck to my fridge. I will take it down when I can recite every word from memory.
That is a fantastic idea Paul! I love it!!
@Paul Wells, I’m honored!
Thanks for the very practical inputs !
You are very welcome!
This is a great article. I have 40+ years in hardware design and development, and everything here rings true, especially:
and
Oh, and checking everything (at least) twice, and, ideally, involving a 3rd party in checking/validation is a more than worthwhile up-front cost in time and money.
Thank you Andy! I agree that Dave wrote a great article. That’s fantastic that your experience matches his, as does mine.
Thanks for the kind words @Andy McClelland!
your pdf idea is great, but the one you have shows some of your markups. not sure this is what you intended
Definitely didn’t mean to include the markups, thanks for letting me know. I didn’t realize the markups in Word would save in a PDF file. I just fixed it. Thanks again!