10 Mistakes To Avoid When Designing a Product Enclosure for Mass Production
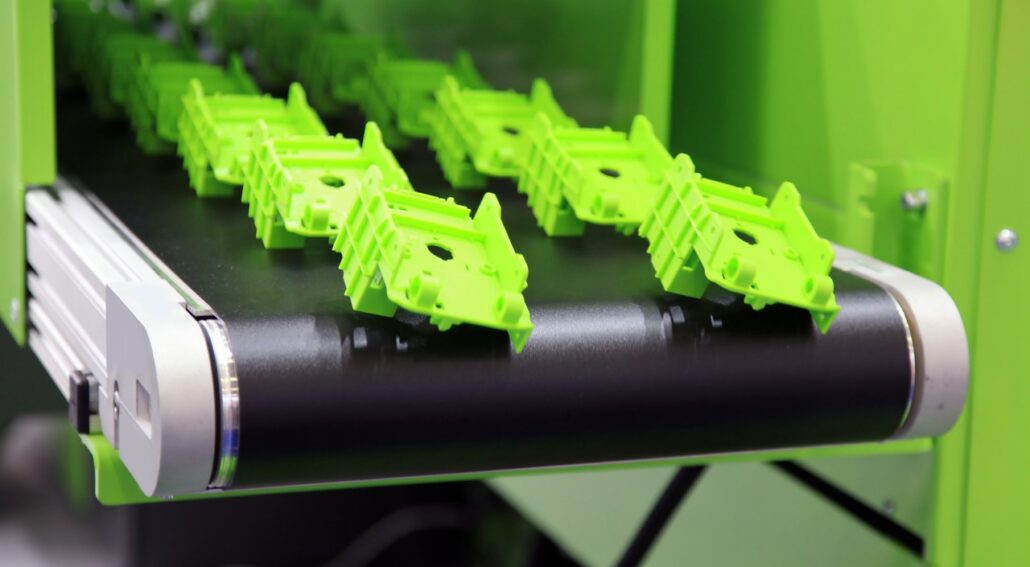
This article is a guest post by Alex Berrou who is a mechanical design engineer, and one of the experts available to help you inside the Hardware Academy.
The beginning of mass production can be one of the most daunting steps in the design of a new product, both for the immediate cost involved and the limitations that it imposes – from there on, the cost of any mistake will be multiplied.
Furthermore, it requires new contacts with previously unnecessary suppliers, most often in other countries.
The challenges of designing an electronic enclosure for manufacturing are very different from those of a prototype or limited-run production.
Here are some of the most common obstacles that can trip up first-time designers as well as veterans of the field.
#1 – Starting Too Early
The simplest and best piece of advice pertaining to mass production is to hold off as long as possible.
That is because, as stated above, mass production will considerably diminish your flexibility in the design of your product.
In a prototype phase, a design adaptation may involve a few hours of CAD and an overnight 3D print.
That same change, in its industrial phase, could require multiple rounds of communication and negotiation, multi-thousand-dollar mold machining and several weeks of work.
Many entrepreneurs want to rush to production in order to commence economies of scale.
This, along with the obtention of a patent, are often pushed by investors beyond logic or practicality. But rushing into a full utility patent isn’t a wise decision.
Excessively enthusiastic industrialization is more likely to impose needless costs and delays into the design process.
What is the solution, then? Quite simply, to hold off on mass production for as long as the product is not entirely, 100% tested and validated by clients in its final form and shape.
Small-batch means of production, chief amongst them 3D printing, are your best friends in this case.
There is no excuse not to make a few dozen prototypes for public testing now that the technology keeps becoming more accessible.
Which is not to say that you should not contact manufacturers along the way. Most will offer free quotes and optimization advice to potential clients.
#2 – Rushing the Design Phases
One of my recent clients had a very accurate idea of what he wanted, including drawings and schematics of the final shape.
Which was very well, until I finished a fully detailed injectable design and discovered that he had not tested the ergonomics beforehand.
The overall shape, once painstakingly 3D printed, was unusable. I had to restart the entire design from scratch, using a far simpler printable design in order to validate the overall shape before moving on to the details.
This, of course, cost the client quite a lot of time and money.
This is a continuation of the first point: all of the classical design phases exist for a good reason, and none should ever be rushed. Think of your project like a house, being built from the foundations up.
If you missed something at the base, it will be vastly more complicated to fix once the floors above are finished. You may even have to tear the whole thing down.
In practice, this means beginning with the aspects that will influence your product’s shape most heavily, and cannot be altered: ergonomics, location and choice of the electronic and mechanical components, functionality.
Other aspects, such as mechanical resistance and above all aesthetics, can be discussed once these foundations are consolidated.
They will be far easier to tweak when starting from a stable base.
#3 – Optimizing the First Design
There is an expression in France that roughly translates to “best is the enemy of good.”
It is a reminder that trying to attain perfection can often come at the cost of more basic aspects, thus imperiling the whole project.
Perfection is seldom obtained on a first run. It is the end result of lots of dull work along with optimization and compromises, and of course lots of real feedback from customers.
A classic example of this is miniaturization. I have had many clients asking to minimize the volume of their product at all costs.
In practice this can mean matching the shape of the enclosure as closely as possible to the electronics, thinning the walls, and other space saving engineering tricks.
A startling but unsurprising number of miniaturized versions of products, due to manufacturing defects and tolerances, wind up with enclosures that will not close, or that even break in use.
All for a few millimeters gained.
A much wiser approach is to assume that things may change in the future, or that reality will not live up to the perfect CAD representation on your screen.
Things like flexibility and adaptability are also, after all, part of a “perfect” product.
#4 – Improvising
Unnecessarily improvising is a problem that applies to all product design, but even more so to mass production.
It’s a common reflex to begin the design of the enclosure with only the most important aspects and components in mind, thinking that the details can be added down the line.
Will this work? Generally, yes.
Is it ideal? Almost never.
Improvising solutions as you design will impose unnecessary compromises, which will not only complexify the design itself but often diminish its functionality.
In the best of cases, it will be a waste of time – think of the house analogy above.
A running gag in my work, for instance, is that I almost always forget to account for the screws or other means of closing the enclosure when making the initial design.
Needless to say, there is seldom enough room left once the enclosure is fully designed around the pcb, which imposes some heavy redrawing.
It is very important to think your design through before booting up the CAD. Map out all of the components, all of the functions required, and create a clear mental image of the finished product.
Not just its appearance, but its function. How will it be used?
How will it be assembled?
Where do you fit the plugs, the batteries?
Once you have a clear idea, take all of the CAD files for the components, drawing those that can’t be found online, and place them in their definitive positions in the CAD model.
Only once this is finished should you start drawing the enclosure itself around the components.
#5 – Putting Function Above Form
Remember, form is relative, but function is absolute. Form is judged on a scale but function is a yes/no question.
A product with a sub-par appearance may be hard to sell, but not as hard as a product that doesn’t work, or can’t be manufactured!
The most common mistake here is to spend hours upon hours perfecting the appearance of your product, only to discover that no known form of production can make it for a reasonable price.
In most cases, you will be aiming for injection molding technology to produce your enclosure. As taught in this article, this technology imposes severe limitations in terms of shapes that can be produced.
You must always keep in mind the challenges of manufacturing when designing your enclosure. This, of course, requires experience and knowledge of the technologies involved.
This can be easy in some cases. The tricks to designing a 3D printable part can be learned in a week of online tutorials and some trial and error.
Injection molding, meanwhile, requires years of experience to master.
#6 – False Assumptions
Never assume anything about the use cases of your product, except for the worse.
Think of it as Murphy’s law of product design – for every condition you expect your product to be exposed to, there is a client who will find a different way to break it, and then complain about it.
Don’t think, “how will an average person use this product?”
Instead, ask “what are the worst conditions that this product will ever, realistically, be exposed to?”
You will be surprised.
The baseline for my enclosure designs is to imagine that it will be exposed to the low and high failure temperatures of the internal electronics, that they will be run over by a car at some point, and that someone will try to use it in driving rain.
And that’s the baseline.
Remember, a product that works only exactly as it should is a defective product.
Smartphones are rarely rated for water exposure, and yet nobody expects theirs to break down on an average rainy day.
Even normal city cars are stress-tested in the Mojave desert and Finnish permafrost, for the simple reason that these are the harshest conditions physically available on the planet.
#7 – Not Accounting for the Fabrication Method
As mentioned, each manufacturing method has its own challenges that must be taken into account during the design.
Some are highly flexible. SLS and SLA printing will let you get away with a lot, while learning the ropes to FDM printing is fairly straightforward.
Others will require an extremely specific design. Machining takes months to master in the field, and injection molding is a full-time profession.
This means that, for one, the manufacturing method must be taken into account from the initial phases of design.
Adapting a pre-existing design for a given fabrication method is almost guaranteed to output sub-par results.
For ideal results, most projects should pass by two different designs.
One for 3D printing, which should be optimized for easy prototyping and iterative modifications, up to small batch manufacturing.
And a second, for the final production method, which should be optimized for functionality and cheap mass production.
These may, in many cases, be very different in appearance, particularly if you rely on FDM printing which has its specific optimal shapes.
If you are skilled in CAD, designing the first version yourself is entirely possible. But you will definitely require a professional’s help for the second.
#8 – Cutting Corners
All sorts of imperfections can be tolerated when making a prototype or short-run product.
A 3D printed part can be corrected after printing, minor imperfections can be smoothed over with a bit of work.
This does not apply to mass production.
For one, mass production relies on the minimizing of human labor. You cannot afford for a person to manually intervene on every part.
The production machines involved in manufacturing are often far more accurate, thus any small visual defects may be more likely to be noticeable.
Their higher speed means that they have far less tolerance in terms of geometry. And any changes will require a long and costly modification and reset.
To recap, a 3D file meant for mass production must be perfect in every way. There is no margin for error or cutting corners.
As detailed above, this is not something that can be easily obtained on a first try, but rather with careful and progressive optimization.
Patience is the key, along with perfectionism. Even minor improvements will save a considerable amount of time and money in the end.
#9 – Straight to International Mass-Sourcing
When comparing prices between manufacturing in western nations and others (e.g. China), it can be tempting to outsource as early as possible.
And while outsourcing is basically a necessity in modern manufacturing (except for cases where “made locally” can justify a doubling of the final price), relying on it too early in a product’s design is definitely a mistake.
This applies even once the prototyping stages are complete.
The early phases of production will generally remain unpredictable, with uneven results and the occasional changes.
And while communication with Chinese factories has greatly improved in quality and ease these last few years, there is still a months-long delivery delay to be accounted for.
This can severely limit your ability to adapt to early issues.
By contrast, local manufacturers can prove far more flexible, even if their costs are higher.
This is invaluable during the early phases of a product’s design, and will allow you the flexibility to change your production quantities while applying corrections to the early design.
Outsourcing abroad will be safer once your market and design are both fully validated.
#10 – Doing Too Much Yourself
A quick disclaimer – I am obviously biased here, being a freelance designer specializing in manufacturing design, but this point is based on observation and experience.
As said, designing the early prototypes of your product for 3D printing can be doable if you have experience in CAD. It is a valid way to minimize your budget, at least.
However, the challenges of mass production require technical experience that cannot be easily obtained. The geometric constraints are multiplied and far more factors have to be taken into account.
Minimum and maximum wall thicknesses and variances, draft angle and allowable overhangs, side-action design, etc..
Meanwhile, the cost of any mistake is multiplied by several orders of magnitude. A minor defect in a 3D print requires a scalpel or some glue.
The same in an injection mold requires heavy lifting equipment, a fully-equipped machining workshop and dozens of work-hours.
You will save far more time and effort by hiring an expert for your production design, or at the very least getting their feedback throughout your design process.
In most cases, the cost of designing an injectable product will be less than that of the initial mold, not to mention the actual production costs and potential modifications.
Final Advice
You will notice a common trend in most of these mistakes – they result from attempts to rush the production design process.
Speed is your enemy in such a high-criticality task, since even the slightest imperfection will have high knock-on costs when it comes to manufacturing.
The key to a good design is to have a pragmatic and methodical approach, carefully thinking through every stage before moving on to the next one.
Use external resources, such as the Hardware Academy’s forums, when you are in doubt. Seek advice and expertise at all times, and do not hesitate to hire experts.
Any delay that you might resent will nonetheless be shorter than the production delays caused by undetected issues, and well worth it in financial terms.
While this list of mistakes applies chiefly to enclosure design, a lot of this advice can also be used for your overall product design.
Caution and patience will serve you well in the choice of your electronics, market and much more.
A few months’ difference will rarely impact the final value of a product, but a detailed approach to the economic and technical challenges involved definitely will impact the product’s value!
Great list of common mistakes, Alex.
I see people send CAD files to manufacturers without specifying basic requirements such as what plastic material, what grade of steel (or how many shots in the tool’s lifetime), and they let the manufacturer guess way too much.
Another huge mistake, on the legal side, is to send money for tooling fabrication without ensure it’s very clear (in an enforceable contract) who owns the tooling.
I was expecting that reliability issues might be overlooked, but you did a nice job covering expected vs. extreme usage & environment.
Thank you Renaud for sharing your always super insightful and helpful advice!
I would add at the end from 50yrs as a natural born innovator, administrator, and analyst
to much of good thing will always turn into a bad thing and to much of a bad thing. Always require not pouring more money into fixing the problem but applying innovation and a lot of collaboration from both your employee but applying good customer service to get your customer base to help be part of the solution. When what they want is no longer in your area of control.
The day you let money or self interest drive the agenda. The odds are you will not be open too the first one, as what you conceived on paper to get the startup money well usually need to change to deal with a changing marketplace or a competitor that in most cases will be someone that see you as a threat or an asset and more money & resource and these days more than willing to us social media to create customer doubt. Too gain their trust. But may not be able to deliver quality.